Технология производства силикохрома
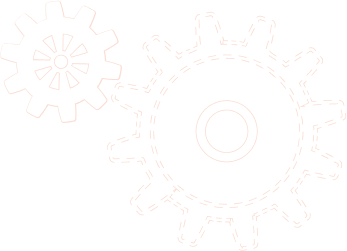
Производство силикохрома SiCr ведут либо бесшлаковым либо шлаковым методом в открытых печах (их мощность составляет от 0,5 до 30 МВА) с вращающейся или стационарной ванной и угольной футеровкой. Диапазон рабочего напряжения: от 145 до 172 В.
Техпроцесс бесшлакового метода выплавки SiCr схож с технологией выпуска ферросилиция. В ходе плавки кремний, который восстановлен из кварцита, разрушает карбиды железа и хрома из передельного феррохрома. Совместное восстановление кремнезема и хромита FeCr2O4 (содержание хрома составляет около 46,5 %) в ходе шлакового процесса происходит по такой схеме:
- образуется сплав Fe с небольшим содержанием окиси углерода;
- усваивается сплав хрома с повышением содержания углерода;
- сплав усваивает кремний, при этом процент углерода снижается в ходе реакций, при которых FeC2 превращается в ферро-силиций и окись углерода;
- образуется карборунд.
В состав колоши шихты при выплавке ферросиликохрома (с 50 % Si) с использованием бесшлакового метода входят 300 килограммов сухого коксика, 135—140 килограммов передельного феррохрома и 10—20 килограммов стружки Fe. При этом схема обслуживания колошника печи при выплавке силикохрома такая же, как при выпуске ферросилиция. В ходе выплавки 50 %-ного ферросиликохрома ванна печи вращается со скоростью 1 оборот за 60 часов. Важно в ходе работы печи обеспечить глубокую (больше 1200 мм) и устойчивую посадку электродов, чтобы создать оптимальные условия для очистки ферросиликохрома от углерода. Сплав выплавляют 4—5 раз за 1 смену в ковш, который футерован шамотным кирпичом.
Химический состав силикохрома таков:
- для раскисления стали:
марка ФСХ 18 - не меньше 18 % кремния и 45 % углерода, не более 3,5 % углерода, 0,06 % фосфора, 0,04 % серы;
марка ФСХ 30 - не меньше 30 % кремния и 40 % углерода, не более 1 % углерода, 0,05 % фосфора, 0,04 % серы;
марка ФСХ 40 - не меньше 40 % кремния и 30 % углерода, не более 0,1 % углерода, 0,04 % фосфора, 0,04 % серы;
- для получения рафинированного феррохрома:
марка СиХрП - 44-55 % кремния и 28 % углерода, 0,027 - 0,1 % углерода, 0,04 % фосфора.
Стоит отметить, что процент углерода в сплаве уменьшается по мере увеличения периода выдержки сплава в ковше и увеличения содержания кремния, поскольку карбид кремния не растворяется в ферросиликохроме и всплывает из сплава в виде силикоуглерода. По этой причине приходится выдерживать сплав в ковше перед тем, как осуществлять его разливку, а затем гранулировать или разлить в слитки.
Выплавку ФСХ18 производят на пониженном колошнике, при этом толщина слоя шихты составляет 130 — 150 сантиметров, глубина посадки электродов равна 50 — 70 сантиметров. В состав шихты входят кварцит (25 — 30 %, фракция 50 — 20 мм), коксик (14—15 %, фракция 8 мм), передельный феррохром (около 49 %) и железная стружка (от 7 до 10 %). При этом избыток твердого углерода равен 3—5 % от всей шихты. Небольшая температура восстановления низкопроцентного силикохрома и отличный показатель газопроницаемости колошника оказывают положительное влияние на ход плавки. В процессе работы ферросплавной печи следует постоянно наблюдать, чтобы посадка электродов была глубокой и устойчивой; иначе температура на подине печи будет снижаться, нормальный выход шлака и силикохрома будет нарушен, процент углерода в сплаве резко возрастет.
В настоящее время чаще применяется шлаковый метод выпуска силикохрома, который обеспечивает оптимальное качество сплава. Он основан на том, что для сплава с содержанием углерода 0,02 % достаточным содержанием в сплаве является 45 % кремния вместо 53 %, это соответствует бесшлаковому методу. Соответственный рост процента хрома в сплаве, уменьшение трудозатрат после того, как исключен добавочный передел, и высокий процент использования хрома гарантируют экономичность всего процесса, который ведется в открытых печах (мощность 10 МВА, рабочее напряжение 130—140 Вольт).
На американском предприятии, построенном в Беверли, к примеру, плавку производят в печи, мощность которой составляет 9 МВА (процесс производят в треугольной ванне). На печи угольная футеровка, а диаметр электродов составляет 890 миллиметров.
В состав колоши шихты входят согласно утвержденному технологическому процессу 230 килограммов кварцита, 248 килограммов хромовой руды (кусковой), 230 килограммов коксика (размер фракции: 12 — 25 мм) и 58 килограммов древесной щепы. Рабочее напряжение равно 145 Вольт, сила тока - 39 кА, электрод погружается в шихту на глубину 90 сантиметров, расстояние от концов электродов до половины составляет 1,4 метра.
Кратность шлака равна 0,8, при этом в нём содержится 44— 48 % оксида углерода, 17—22 % окиси алюминия, 29—30 % оксида магния и 0,5 % оксида хрома, а в сплаве около 43 % кремния, 40% хрома и 0,03 % углерода.
К кварциту и углеродистому восстановителю те же требования, что и в производстве ферросилиция, однако ужесточаются требования по содержанию в коксике серы. В донских хромовых рудах для выпуска ферросплавов должно быть 50 % оксида хрома, Cr2O3/FeO должно быть выше 3, содержание окиси Si больше 7 %, а фосфора - менее 0,008 %. Порошковые руды и концентраты, которые получены в ходе обогащения бедных руд, не всегда можно с высокой эффективностью использовать в плавке, из-за этого необходимо провести их окускование. В извести для выплавки сплавов хрома должно быть больше 90 % окиси кальция и до 0,01 % фосфора.
Техпроцесс бесшлакового метода выплавки SiCr схож с технологией выпуска ферросилиция. В ходе плавки кремний, который восстановлен из кварцита, разрушает карбиды железа и хрома из передельного феррохрома. Совместное восстановление кремнезема и хромита FeCr2O4 (содержание хрома составляет около 46,5 %) в ходе шлакового процесса происходит по такой схеме:
- образуется сплав Fe с небольшим содержанием окиси углерода;
- усваивается сплав хрома с повышением содержания углерода;
- сплав усваивает кремний, при этом процент углерода снижается в ходе реакций, при которых FeC2 превращается в ферро-силиций и окись углерода;
- образуется карборунд.
В состав колоши шихты при выплавке ферросиликохрома (с 50 % Si) с использованием бесшлакового метода входят 300 килограммов сухого коксика, 135—140 килограммов передельного феррохрома и 10—20 килограммов стружки Fe. При этом схема обслуживания колошника печи при выплавке силикохрома такая же, как при выпуске ферросилиция. В ходе выплавки 50 %-ного ферросиликохрома ванна печи вращается со скоростью 1 оборот за 60 часов. Важно в ходе работы печи обеспечить глубокую (больше 1200 мм) и устойчивую посадку электродов, чтобы создать оптимальные условия для очистки ферросиликохрома от углерода. Сплав выплавляют 4—5 раз за 1 смену в ковш, который футерован шамотным кирпичом.
Химический состав силикохрома таков:
- для раскисления стали:
марка ФСХ 18 - не меньше 18 % кремния и 45 % углерода, не более 3,5 % углерода, 0,06 % фосфора, 0,04 % серы;
марка ФСХ 30 - не меньше 30 % кремния и 40 % углерода, не более 1 % углерода, 0,05 % фосфора, 0,04 % серы;
марка ФСХ 40 - не меньше 40 % кремния и 30 % углерода, не более 0,1 % углерода, 0,04 % фосфора, 0,04 % серы;
- для получения рафинированного феррохрома:
марка СиХрП - 44-55 % кремния и 28 % углерода, 0,027 - 0,1 % углерода, 0,04 % фосфора.
Стоит отметить, что процент углерода в сплаве уменьшается по мере увеличения периода выдержки сплава в ковше и увеличения содержания кремния, поскольку карбид кремния не растворяется в ферросиликохроме и всплывает из сплава в виде силикоуглерода. По этой причине приходится выдерживать сплав в ковше перед тем, как осуществлять его разливку, а затем гранулировать или разлить в слитки.
Выплавку ФСХ18 производят на пониженном колошнике, при этом толщина слоя шихты составляет 130 — 150 сантиметров, глубина посадки электродов равна 50 — 70 сантиметров. В состав шихты входят кварцит (25 — 30 %, фракция 50 — 20 мм), коксик (14—15 %, фракция 8 мм), передельный феррохром (около 49 %) и железная стружка (от 7 до 10 %). При этом избыток твердого углерода равен 3—5 % от всей шихты. Небольшая температура восстановления низкопроцентного силикохрома и отличный показатель газопроницаемости колошника оказывают положительное влияние на ход плавки. В процессе работы ферросплавной печи следует постоянно наблюдать, чтобы посадка электродов была глубокой и устойчивой; иначе температура на подине печи будет снижаться, нормальный выход шлака и силикохрома будет нарушен, процент углерода в сплаве резко возрастет.
В настоящее время чаще применяется шлаковый метод выпуска силикохрома, который обеспечивает оптимальное качество сплава. Он основан на том, что для сплава с содержанием углерода 0,02 % достаточным содержанием в сплаве является 45 % кремния вместо 53 %, это соответствует бесшлаковому методу. Соответственный рост процента хрома в сплаве, уменьшение трудозатрат после того, как исключен добавочный передел, и высокий процент использования хрома гарантируют экономичность всего процесса, который ведется в открытых печах (мощность 10 МВА, рабочее напряжение 130—140 Вольт).
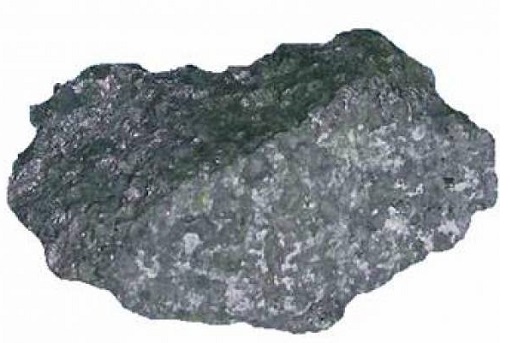
В состав колоши шихты входят согласно утвержденному технологическому процессу 230 килограммов кварцита, 248 килограммов хромовой руды (кусковой), 230 килограммов коксика (размер фракции: 12 — 25 мм) и 58 килограммов древесной щепы. Рабочее напряжение равно 145 Вольт, сила тока - 39 кА, электрод погружается в шихту на глубину 90 сантиметров, расстояние от концов электродов до половины составляет 1,4 метра.
Кратность шлака равна 0,8, при этом в нём содержится 44— 48 % оксида углерода, 17—22 % окиси алюминия, 29—30 % оксида магния и 0,5 % оксида хрома, а в сплаве около 43 % кремния, 40% хрома и 0,03 % углерода.
К кварциту и углеродистому восстановителю те же требования, что и в производстве ферросилиция, однако ужесточаются требования по содержанию в коксике серы. В донских хромовых рудах для выпуска ферросплавов должно быть 50 % оксида хрома, Cr2O3/FeO должно быть выше 3, содержание окиси Si больше 7 %, а фосфора - менее 0,008 %. Порошковые руды и концентраты, которые получены в ходе обогащения бедных руд, не всегда можно с высокой эффективностью использовать в плавке, из-за этого необходимо провести их окускование. В извести для выплавки сплавов хрома должно быть больше 90 % окиси кальция и до 0,01 % фосфора.