Способы разливки ферросплавов
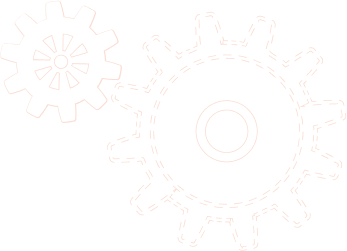
Разливка металла в современном производстве ферросплавов производится несколькими наиболее распространенными методами: с помощью специализированных машин для разливки; в неподвижные металлические формы и поддоны; в установленные на пол изложницы слой за слоем или в литейные канавы одну плавку за другой.
Использование конвейера в литейном производстве ферросплавов представляет наиболее перспективную методику разливки. Такие машины используются при разливке силикомарганца, углеродистого ферромарганца, ферросилиция и, изредка, феррохрома. Дополнительным преимуществом данной методики является рост производственной мощности, высокая механизация и снижение доли ручного труда, а также оптимизация трудовых условий в разливочном промежутке, так как вместо тяжеловесных кранов используют гидравлические кантователи, помещенные в герметичные камеры. Однако ввиду варьирования уровней высоты падения металла во время разливки, отмечается образование сильных брызг, что является значительным недостатком конвейерной машины. В этой связи при разливке сплавов в предварительно обрызганные известковым молоком изложницы конвейера теряется порядка 3 % материала, а его товарный вид ухудшается.
Конвейерно-тележечные карусельные машины позволяют получать слитки металла более высокого качества и товарного вида, а также сократить процент потерь сырья при разливке. Такие механизмы используют в производстве сплавов с легкоокисляющимися компонентами, лигатур, высококремнистых металлов и модификаторов. Готовые слитки получаются тонкими благодаря разливке в расположенные на конвейере тележки с мульдами, которые движутся по замкнутой цепи.
Чтобы извлечь готовые слитки из мульд, тележки переворачивают, а в некоторых случаях слитки выталкивают в резервуар под изложницей с помощью толкателя. Неподвижные металлические формы или массивные поддоны в настоящее время мало используются в ферросплавном производстве.
Как правило, этой устаревшей методикой пользуются в цехах металлотермических или оборудованных рафинировочными печами. Такой способ разливки требует расширения площади цеха, чтобы установить стационарные формы, он сопряжен с высокой температурой воздуха в цехе и чрезмерно перегружает разливочные краны. Тем не менее, кристаллизаторы или большие поддонники целесообразно использовать для разливки сплавов, имеющих тенденцию к сегрегации, в слитки толщиной не более 8 см. К таким металлам, в частности, можно отнести ферросилиций, содержащий более 75 % Si.
Одним из принципиально важных моментов в производстве ферросплавов является методика разделение готового металла и шлака. В зарубежных странах практикуют разливку из печей через две отдельные летки для выпуска сплава и шлака. Если в печах предусмотрена только одна летка, металл выливают в специальный ковш, наполняя его через верх, таким образом, шлак отделяется сам или посредством скиммера (специального приспособления для отсортировывания шлака). Методика наполнения ковша с переливом позволяет проводить более контролированный процесс, поскольку поток жидкого металла можно регулировать. При этом металл в слитках получается более плотный и чистый. Вместе с тем, такая технология предусматривает большие материальные затраты на оборудование разливочного отрезка больших размеров, эксплуатацию мостовых кранов с высокой грузоподъемностью и ковшовых тележек.
Скиммер для отделения шлака, равно как передвижной, так и неподвижный, позволяет сократить площадь помещения цеха и избежать использования мостовых кранов. При этом площадь требуется лишь для установки самого скиммера и желобов, по которым будет подаваться металл. Направление движения жидкого металла можно задать непосредственно в разливочный механизм. Побочным эффектом такой системы является возможное засорение желобов шлаком и отходами, которые высыпаются в отвал. Тем не менее, за счет оптимальной компоновки оборудования в цеху можно уменьшить ширину помещения, если из печи сплав подается на разливочный участок по желобам через скиммер.
Для дальнейшей переработки ферросплавы проходят процедуру рассева и дробления, то есть разделяются на мелкие части. От твердости ферросплава зависит вид дробилки для его измельчения. В практике зарубежных производителей ферросплавы сортируются по размеру зерна, то есть фракционируются. Подобные стандарты приняты и в отечественной промышленности. В дальнейшем использование в сталеплавильных цехах ферросплавов определенных размеров позволяет сократить потери тепла металла в ковшах, а также ускоряют приобретение жидкой сталью легирующих свойств.
Различают порошковый (толщина зерна до 0,2 см), зернистый (зерно от 0,2 до 1 см) и кусковый (величина куска более 1 см) виды ферросплавов. Для получения порошкообразной массы готовый остывший металл сильно измельчают в дробилке или гранулируют, то есть в жидком состоянии распыляют паром или инертным газом. Спрос на гранулированные ферросплавы обусловлен возможностью беспрерывной загрузки такого сырья в сталеплавильные печи.
Использование конвейера в литейном производстве ферросплавов представляет наиболее перспективную методику разливки. Такие машины используются при разливке силикомарганца, углеродистого ферромарганца, ферросилиция и, изредка, феррохрома. Дополнительным преимуществом данной методики является рост производственной мощности, высокая механизация и снижение доли ручного труда, а также оптимизация трудовых условий в разливочном промежутке, так как вместо тяжеловесных кранов используют гидравлические кантователи, помещенные в герметичные камеры. Однако ввиду варьирования уровней высоты падения металла во время разливки, отмечается образование сильных брызг, что является значительным недостатком конвейерной машины. В этой связи при разливке сплавов в предварительно обрызганные известковым молоком изложницы конвейера теряется порядка 3 % материала, а его товарный вид ухудшается.
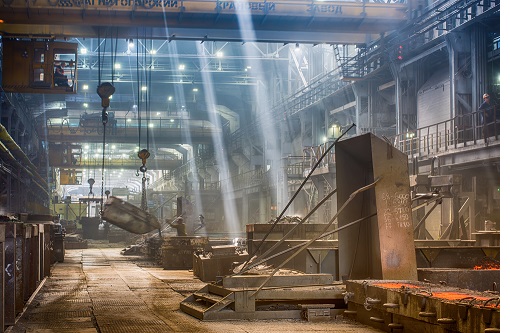
Чтобы извлечь готовые слитки из мульд, тележки переворачивают, а в некоторых случаях слитки выталкивают в резервуар под изложницей с помощью толкателя. Неподвижные металлические формы или массивные поддоны в настоящее время мало используются в ферросплавном производстве.
Как правило, этой устаревшей методикой пользуются в цехах металлотермических или оборудованных рафинировочными печами. Такой способ разливки требует расширения площади цеха, чтобы установить стационарные формы, он сопряжен с высокой температурой воздуха в цехе и чрезмерно перегружает разливочные краны. Тем не менее, кристаллизаторы или большие поддонники целесообразно использовать для разливки сплавов, имеющих тенденцию к сегрегации, в слитки толщиной не более 8 см. К таким металлам, в частности, можно отнести ферросилиций, содержащий более 75 % Si.
Одним из принципиально важных моментов в производстве ферросплавов является методика разделение готового металла и шлака. В зарубежных странах практикуют разливку из печей через две отдельные летки для выпуска сплава и шлака. Если в печах предусмотрена только одна летка, металл выливают в специальный ковш, наполняя его через верх, таким образом, шлак отделяется сам или посредством скиммера (специального приспособления для отсортировывания шлака). Методика наполнения ковша с переливом позволяет проводить более контролированный процесс, поскольку поток жидкого металла можно регулировать. При этом металл в слитках получается более плотный и чистый. Вместе с тем, такая технология предусматривает большие материальные затраты на оборудование разливочного отрезка больших размеров, эксплуатацию мостовых кранов с высокой грузоподъемностью и ковшовых тележек.
Скиммер для отделения шлака, равно как передвижной, так и неподвижный, позволяет сократить площадь помещения цеха и избежать использования мостовых кранов. При этом площадь требуется лишь для установки самого скиммера и желобов, по которым будет подаваться металл. Направление движения жидкого металла можно задать непосредственно в разливочный механизм. Побочным эффектом такой системы является возможное засорение желобов шлаком и отходами, которые высыпаются в отвал. Тем не менее, за счет оптимальной компоновки оборудования в цеху можно уменьшить ширину помещения, если из печи сплав подается на разливочный участок по желобам через скиммер.
Для дальнейшей переработки ферросплавы проходят процедуру рассева и дробления, то есть разделяются на мелкие части. От твердости ферросплава зависит вид дробилки для его измельчения. В практике зарубежных производителей ферросплавы сортируются по размеру зерна, то есть фракционируются. Подобные стандарты приняты и в отечественной промышленности. В дальнейшем использование в сталеплавильных цехах ферросплавов определенных размеров позволяет сократить потери тепла металла в ковшах, а также ускоряют приобретение жидкой сталью легирующих свойств.
Различают порошковый (толщина зерна до 0,2 см), зернистый (зерно от 0,2 до 1 см) и кусковый (величина куска более 1 см) виды ферросплавов. Для получения порошкообразной массы готовый остывший металл сильно измельчают в дробилке или гранулируют, то есть в жидком состоянии распыляют паром или инертным газом. Спрос на гранулированные ферросплавы обусловлен возможностью беспрерывной загрузки такого сырья в сталеплавильные печи.