Разливка под защитными средами
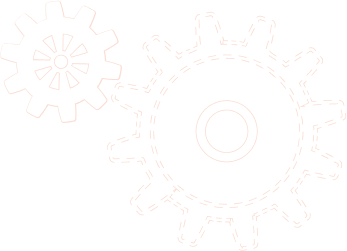
В момент разливки происходит окисление кислородом струи и металла. Чтобы уберечь металл от процесса окисления в момент разливки следует применять: нейтральный газ, синтетический шлак, петролатум и др. Нейтральным газом, зачастую, является аргон.
За последний период популярностью стало пользоваться разливка стали под жидким синтетическим шлаком, который наводится на зеркало металла в кристаллизаторе. Такой процесс влияет на понижение температуры с явной гранью металла, а также способствует обеспечению защиты от окисления кислородом воздуха. Помимо этого, формирующийся слитком и кристаллизатором шлаковый пласт диаметром 0,2-3 мм, выступающий в качестве смазки, делает легче свободную усадку слитка, при этом ослабляет термический удар металла в момент соприкосновения с остывшим кристаллизатором. Выделенные признаки создают условия получения заготовок с плоскостью, не имеющей плен, заворотов и продольных трещин.
Жидкий шлак, в котором содержится 34—40 % CaF2, 35—40 % SiO2, 10—15 % Al2O3 и 10—15 % CaO, производится в дуговой электрической печи из плавикового шпата, шамотного порошка, извести и песка, либо напрямую на плоскости металла в момент применения тепловыделяющего смесей или брикетов. Жидкий шлак заливают в изложницы сверху после появления в них первых порций металла, а экзотермические смеси в бумажных пакетах и брикеты укладывают на дно изложницы до начала разливки. Издержки шлака около 4-5 кг, экзотермических смесей – 4-4,5 кг, а брикетов до 3-5 кг на 1 т стали.
Тепловыделяющие смеси и брикеты, используемые с целью обогрева прибыльной части, приблизительно схожи. Для горючих компонентов можно использовать порошки алюминия, либо силикокальция, а окислителем может выступить селитра, либо руда. Наполнителями веществ, отвечающих за обеспечение важных физико-химических свойств металлургического расплава, принято считать дифторид кальция, песок, доломит и др. Процесс разливки под шлаками из экзотермических смесей и брикетов гораздо проще в организационном плане. Вот почему этот процесс более распространён, по сравнению с технологией, отвечающей за применение синтетического шлака, изготовленного в специально оборудованных печах.
За последний период популярностью стало пользоваться разливка стали под жидким синтетическим шлаком, который наводится на зеркало металла в кристаллизаторе. Такой процесс влияет на понижение температуры с явной гранью металла, а также способствует обеспечению защиты от окисления кислородом воздуха. Помимо этого, формирующийся слитком и кристаллизатором шлаковый пласт диаметром 0,2-3 мм, выступающий в качестве смазки, делает легче свободную усадку слитка, при этом ослабляет термический удар металла в момент соприкосновения с остывшим кристаллизатором. Выделенные признаки создают условия получения заготовок с плоскостью, не имеющей плен, заворотов и продольных трещин.
Жидкий шлак, в котором содержится 34—40 % CaF2, 35—40 % SiO2, 10—15 % Al2O3 и 10—15 % CaO, производится в дуговой электрической печи из плавикового шпата, шамотного порошка, извести и песка, либо напрямую на плоскости металла в момент применения тепловыделяющего смесей или брикетов. Жидкий шлак заливают в изложницы сверху после появления в них первых порций металла, а экзотермические смеси в бумажных пакетах и брикеты укладывают на дно изложницы до начала разливки. Издержки шлака около 4-5 кг, экзотермических смесей – 4-4,5 кг, а брикетов до 3-5 кг на 1 т стали.
Тепловыделяющие смеси и брикеты, используемые с целью обогрева прибыльной части, приблизительно схожи. Для горючих компонентов можно использовать порошки алюминия, либо силикокальция, а окислителем может выступить селитра, либо руда. Наполнителями веществ, отвечающих за обеспечение важных физико-химических свойств металлургического расплава, принято считать дифторид кальция, песок, доломит и др. Процесс разливки под шлаками из экзотермических смесей и брикетов гораздо проще в организационном плане. Вот почему этот процесс более распространён, по сравнению с технологией, отвечающей за применение синтетического шлака, изготовленного в специально оборудованных печах.