География черной металлургии
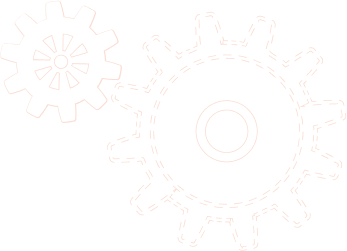
Черная металлургия всегда была и останется основой всей металлургии. Железо, которое является готовой продукцией отрасли, известное нам как чугун, сталь и прокат из нее навсегда останутся массовым материалом потребления во всем мировом хозяйстве. Металл давно вытеснил из строительной индустрии древесину, соперничая лишь с цементом, иногда объединяясь с ним в союз – железобетон. Конечно, строительный мир не стоит на одном месте, и сейчас активно внедряется в строительство такие материалы, как полимер и керамика. Однако, пока что, железо не собирается сдавать свои позиции и держится на торговом рынке лидером продаж.
Говоря о металлургии XXI века, стоит отметить то, что до начала XX века она была очень слабо развита. Основными странами-поставщиками металла на рынок в начале XX века являлись США, Великобритания, Германия и Бельгия. Эти страны поставляли на рынок металлов более 83% от всего товара на рынке. Со временем, после Второй мировой войны, началось активное освоение металлургического комплекса рядом развитых и развивающихся стран. В последнее время мы отчетливо видим тенденция перемещения производства черных металлов из развитых стран в развивающиеся.
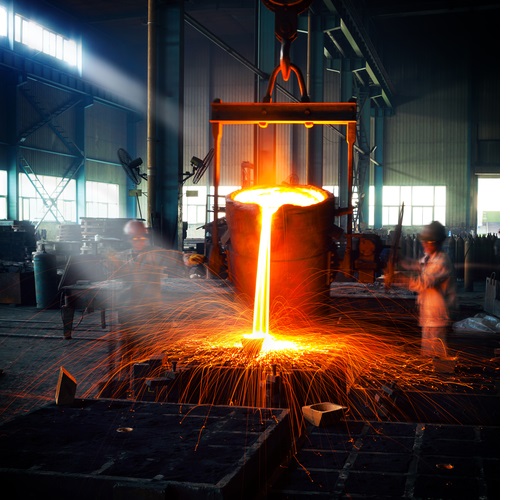
Черная металлургия сильно зависит от многих других отраслей народного хозяйства. Ее сырьевая база — продукция горнодобывающей промышленности (железная руда, известняки, огнеупоры), топливной (коксующийся уголь, природный газ) и электроэнергетика.
Кроме этого, цветная металлургия – смежная черной металлургии, обеспечивает ее поставкой легируюших компонентов необходимых для разнообразных сплавов. Народное хозяйство является основным инструментом получения лома и других отходов для их вторичного использования в металлургических переделах.
ПО технологическому процессу производства черная металлургия имеет тесные связи с некоторыми разновидностями химического производства: коксованием угля, использованием кислорода и ряда инертных газов в процессах плавки материалов и т.д. С транспортной инфраструктурой черную металлургию связывает использование больших объемов сырья, получения готовой продукции и полуфабрикатов.
Производство черных металлов, их добыча и переработка сырья составляют большую опасность для экологии. Выброс газов в атмосферу и загрязнение водоемов – это еще не верхушка айсберга. Большим ударом для экосистемы является наличие отходов от производства, причем отходы невозможно утилизировать. Так самыми вредными отходами являются: канцерогены коксохимического процесса, доменные выбросы, газы и пыль при агломерировании руды, конвертерного и других плавильных агрегатов, шлаки всех металлургических переделов.
В процессе производств используется большое количество воды, температура после ее участия в металлургических процессах изменяется и таким образом, попадание в эту воду отходов промышленности приводит к химическому и температурному нарушению режима естественных источников водоснабжения.
На сегодняшний день, с экономической точки зрения, черная металлургия является одной из малодоходных отраслей обрабатывающей промышленности. Больших вложений капиталов требует развитие всех производств черной металлургии, что обусловлено технологией выпускаемой продукции – большими объемами производства, дороговизной оборудования, финансовыми затратами на его амортизацию и созданием огромной сети заводской инфраструктуры, отвечающей современным требованиям. Затраты предприятий на обеспечение экологической чистоты работы металлургического предприятия могут достигать до 20 % общих капиталовложений.
В настоящее время требования к экологической безопасности в современных условиях, все больше ужесточаются. Как известно, вложенные капиталы в большое производство возвращаются намного медленнее, чем в средний бизнес. Таким образом, находится слишком мало инвесторов, готовых вложить свои деньги в развитие черной металлургии. Несмотря на свою значимую роль в индустрии любой страны, удельный вес черной металлургии, как правило, не превышает- 4-7 %.
Стоимость основной продукции черной металлургии имеет относительно низкую стоимость – от 20 до 400 долларов за одну тонну сырья. Поэтому в настоящее время, собственники металлургических заводов не жалеют денег на поиск способов повышения эффективности производства за счет внедрения новых видов оборудования, развитие более совершенных технологий во всех процессах производства, компьютеризация процессов производства, особенно в доменном и прокатном переделе.
Заметим, что главной причиной по которой происходит внедрение научно-технологического прогресса, является снижение затрат на производство, путем его модернизации. Однако внедрения НТП на производство не позволяет в настоящее время снизить затраты. Как показывает мировая практика, главным путем повышения рентабельности производства, является изменение отраслевой и территориальной структуры черной металлургии, отказ от традиционного комбинирования отдельных производств, повешение уровня их специализации, и, следовательно, сокращение за этот счет величины предприятий и объемов выпускаемой продукции. Вся эта деятельность направлена на большие перестановки, не только на межрегиональном уровне, но и порой влечет за собой межстрановые и внутристрановые сдвиги в размещении самой отрасли и ее производств.
Подобные сдвиги стали особенно заметные в эпоху научно-технической революции, перекроив карту распределения производств черной металлургии по-новому. Но все же, НТП не в состоянии охватить всю отрасль целиком, и поэтому воздействие его воздействие избирательно, в зависимости от конкретных задач и проблем в тех или иных производствах.
В процессах облагораживания железной руды главным на сегодняшний день заданием является получение металлизированных окатышей, что заметно улучшает качество руды для выплавки чугуна. А благодаря внедрению метода прямого восстановления из металлизированных окатышей железа стало возможным вообще отказаться от доменного производства.
Широкое распространение и внедрение в процессы производства в сталеплавильной промышленности получила высокоэффективная кислородно-конвертерная выплавка металла, непрерывная разливка стали. Особое значение в прокатном переделе получил «четвертный передел», значительно повышающий качество конечной продукции для черной металлургии. Заметно сказалось внедрение инновационных процессов на все уровни организации отрасли, прежде всего предприятий, таким образом, воздействовав и на другие отрасли народного хозяйства. Так в результате этих нововведений упростилась перевозка сырья морским транспортом, и привело к большому территориальному разрыву между базами по добыче сырья и предприятиями-потребителями. Получение проката высокого качества, с высокой точностью размеров во множество раз количество потребителей данной продукции, особенно в машиностроительной отрасли.
Большой спрос на продукцию черной металлургии со стороны всех отраслей мирового хозяйства привел к значительному увеличению номенклатуры продукции отрасли. Так, если в настоящее время насчитывается около десятков сортов и марок чугуна, то разновидность стали включает в себя несколько тысяч видов. Количество изделий прокатного производства в развитых странах достигает несколько десятков тысяч видов и размеров. Это привело к необходимости выпуска продукции в сравнительно небольших объемах на узкоспециализированных предприятиях «четвертого передела» и интенсивному внешнеторговому обмену такими видами продукции между многими странами.
Так изменения в технологиях производства, типах используемого оборудования, характера спроса на продукцию отрасли привели к широкомасштабной реконструкции и модернизации на ряде предприятий. Выделим следующее из них:
- в доменном производстве сооружение гораздо более мощных домен;
- в сталелитейном производстве полностью пришлось отказаться от бессемеровского и мартеновского процессов выплавки стали и отказаться от морально устаревшего оборудования по разливу стали.
Все это и привело к формированию нового состава предприятий. Традиционное для этой отрасли комбинирование производства всех металлургических переделов стало испытывать все большее воздействие процессов специализации металлургических заводов. Создание мини – и мидизаводов производственной мощностью в 0,1-1,0 млн. т металлопродукции в год привело к гибели крупных заводов. Ничего удивительного при состоянии нынешней мировой экономике в этом нет. Так предприятия малой и средней мощности требуют намного меньше капиталовложений, более коротких сроков строительства завода, простой инфраструктуры, число людей работающих на предприятии намного меньше, стало возможным внедрение автоматизирование основных производственных процессов и создании более благоприятных экологических условий производства. В основном узкоспециализированные заводы неполного металлургического цикла вырабатывают качественные стали и разнообразный сложный прокат. Они для своих электродуговых печей обычно используют ресурсы местного металлолома, а выпускаемый ими прокат высокой стоимости расходится в стране и за ее пределами.
Современная география
В черной металлургии всегда господствовали крупные компании, обладающие необходимыми средствами для инвестиций в строительство новых предприятий и техническое перевооружение старых. Они менее болезненно переносят неустойчивость мирового рынка черных металлов, выдерживают высокую конкуренцию, быстрее остальных внедряют инновационную продукцию.
Виды собственности металлургической отрасли в разных странах имеют неодинаковую форму. В одних они полностью принадлежат частным владельцам, акционерным компаниям, в других — государству, а в некоторых возможно комбинирование, при котором базовый пакет акций принадлежит государству, а 25-40% частным лицам. В наши дни стало распространенной практикой совместного владения предприятиям национального и иностранного капитала.
Исторически черная металлургия сложилась как отрасль индустрии с очень большой мощностью оборудования. Особенно велика концентрация в выплавке чугуна и стали, где сам характер производства определяет очень крупные агрегаты, мощность которых продолжает расти. В прокатном производстве, особенно на заключительных стадиях передела, она намного меньше. Именно в области прокатного производства вырастают все новые малые и средние предприятия, создающие фирмы, совсем не связанные организационно с крупнейшими металлургическими монополиями.
В эпоху НТР наблюдалось снижение металлоемкости народного хозяйства за счет существенного повышения качества металла, конкуренции пластмасс и синтетических смол, ряда цветных металлов оказало сильное воздействие на все развитие черной металлургии и изменение всех ее отраслевых структур. Во многом структуру отрасли определяет целый ряд различных производств, отличающимися друг от друга продукцией, техническим оснащением предприятия и технологией производств, направлением ее использования как внутри страны, так и за ее пределами.
На сегодняшний день в структуре отрасли черной металлургии выделяются следующие производства:
Сырьевое производство – охватывающий такой ряд действий как добыча и обогащение железной руды, ее агломерирование, сбор металлического лома и подготовка его к переплаву;
Полупродуктовые переделы – включают в себя выплавку чугуна и доменных ферросплавов, а также стали и ее сплавов.
Наиболее важное значение имеют конечные переделы – получение проката и отливок из чугуна и стали.
Добычу вспомогательных материалов, в большинстве стран мира относят к другим отраслям индустрии. Благоприятные изменения в развитии черной металлургии отражает соотношение выплавки стали и чугуна. Так, благодаря увеличившемуся спросу на прокат в машиностроении и строительстве произошли масштабные сдвиги в сторону выплавки стали. Если в начале XX века производство чугуна в мире было в 1,04 раза больше чем стали, то уже в 50-х годах прошлого века производство стали увеличилось в 1,67 раза по отношению к чугуну, так как выплавка была сосредоточена в немногих промышленных государствах мира.
Создание крупных предприятий по производству черных металлов в новых индустриальных странах в период с 50-90 годов XX века привела к значительному снижению этого коэффициента до 1,43. Стоит отметить, что в развитых странах он остается еще высоким – так в Италии он равен 2,37, в США – 1,87 и т.д. В России 1995 г., в результате распада СССР, данный коэффициент с 1,4 упал до 1,28. В КНР в результате острого дефицита черных металлов, главным образом стали и проката из нее, привел к стимулированию выплавки литейного чугуна, что соответственно понизило коэффициент в 1995 г. до 0,91.
Сырьевая база черной металлургии.
Как известно, основным исходным видом сырья в черной металлургии является железная руда. В результате бурного развития НТП были освоены процессы использования руды для непосредственной выплавки стали, минуя стадию получения чугуна, что еще более увеличило роль железной руды во всем металлургическом производстве.
На сегодняшний день железная руда остается одним из широко востребованных видов продукции горнодобывающей промышленности. Так по объемам добычи, железная руда уступает только углю, нефти и природному газу. Одна существует существенный ряд проблем и вопросов, связанных с добычей, обогащением и транспортировкой железной руды, причем проблемы эти более весомые, чем у остальных энергоносителей. Для того чтобы увеличить свои сырьевые запасы железной руды, государства с частными инвесторами проводят геологоразведочные работы. В большинстве своем, на сегодняшний день, основные залежи этого сырья находятся в труднодоступных и ранее неразведанных местах. Так, мировые разведанные запасы железной руды составляют где-то около 160 млрд. тонн, из которых 80 млрд. тонн являются «чистым» железом. Так по данным Геологической разведки США, Россия и Бразилия обладают 18% мировых запасов железа. Таким образом, несмотря на то, что добыча железных руд продолжается и на сегодняшний день, и добыча их возрастает, благодаря, геологической разведке запасы руды возросли.
Количество запасов железных руд в различных странах и регионах мира неодинаково. Самые большие запасы руды, где-то около 28% от мировых запасов, находятся на территории государств Восточной Европы, преимущественно в России и на Украине, 17% на территории Азии – КНР и Индия, по 16% в Южной Америке (крупные месторождения расположены в Бразилии) и Африке, 13% на территории Северной Америки (США, Канада) и по 5-6% в Западной Европе и Австралии. Несмотря на то, что многие страны мира не имеют запасов железной руды отвечающей их потребностям, черная металлургия на их территории развита довольно успешно. Это можно сказать о таких странах, как Япония, Германия, Республика Корея и др.
Одной из проблем черной металлургии является то, что не все железные руды богаты железом. Так существует условное деление руды, в зависимости от диапазона содержания в ней железа:
-богатые руды: в них уровень содержания железа более 50%;
- рядовые руды: уровень железа в пределах 25-50%;
- бедные руды: содержание железа в таком типе руды никогда не превышает 25%.
Во многих высокоразвитых странах мира богатых руд практически нет, так в Западной Европе только Швеция обладает богатыми запасами руды (60-65% железа). Остальная часть рудных ресурсов региона имеет бедные руды. Это послужило главной причиной их добычи и разработки в Великобритании, Германии и Бельгии. Все это произошло из-за того, что ранее, будучи крупными промышленным центрами по добычи руды, эти страны полностью разорили месторождения сырья. Следую примеру мировых лидеров, Франция – одна из богатейших стран сырья, также с 1993 года полностью прекратила добычу этого ресурса. Не только страны Западной Европы столкнулись с этой проблемы. Оскудели по качеству и месторождения железорудного сырья и в Северной Америке. США давно использовали все богатые руды, и теперь перешли на использование рядовых руд, содержащих порядком до 50% железа. На Североамериканском материке пока что Канада и Мексика располагают запасами богатых руд, процент содержания железа в которых равен приблизительно 61-63%.
Такая же проблема постигла и страны расположенные на территории Восточной Европы. Так в среднем процент содержания железа в руде извлекаемой Россией и Украиной составляет не более 40%.
В Азии ситуация остается более терпимой. Так самой богатой рудой обладает Индия, в состав добытой руды входит до 63% железа. КНР не обладает подобными ресурсами, и вынуждено разрабатывать преимущественно бедные руды.
Страны с развитой черной металлургией – Япония и Республика Корея, не имеют вообще собственных ресурсов железной руды. Такая ситуация и определила быстрое перемещение железорудного производства в другие страны разных регионов мира. Качество добываемой руды в таких странах значительно лучше: в Бразилии до 68% железа, в Австралии и Венесуэле – 64%, в Индии – 63% и в ЮАР – 60-65% содержания «чистого» железа. Перечисленные страны обладают крупными запасами для развертывания мощной железорудной промышленности.
Происходящие изменения принесли существенные географические сдвиги в распределении черной металлургии в мире. Так еще в 1938 года доля этих стран в мировой добычи железа составляла 16%, в 1970 г. она возросла до 35%, а уже в 1995 г. – стала добывать ровно половину всех железорудных ресурсов – 55%.
Повысить качество продукта позволило внедрение новых научно-технических методов обогащения бедных и рядовых руд, вводимых в США и странах Западной Европы. Таким образом, в промышленности стали широко применять мелкозернистые руда и они стали пригодными и для домен высокой мощности. Но главным недостатком этих рудных агломератов является их малотранспортабельность, и изготовление проводилось только в районах металлургии.
Намного большее значение для обогащения всех типов руд мело место освоение производства железорудных окатышей, среднее содержание металла в которых доходило до 65-70%. Преимуществом железорудных окатышей являлось то, что они обладали высокой транспортабельностью и помимо доменного производства, нашли еще одну сферу применение – в прямом восстановлении железа. Все это позволило расширить добычу окатышей, в особенности на экспорт.
Кардинальные сдвиги в мировой железорудной промышленности произошли в XX века. До Второй мировой войны ведущими лидерами по разработке и добычи железной руды Западная Европа и США были мировыми лидерами. На долю первых приходилось 55% добычи сырья, вторых – 40%. В 1950 г. после войны, показатели этих двух регионов резко упали: Северная Америка стала давать – 43% железной руды в мире, а Западная Европа – 30%. В 70-80-х гг. прошлого века, лидерами по добычи сырья стали: Восточная Европа, Южная Америка, Азия – на долю каждого экономического региона приходилось от 20 до 30%. Еще одним лидером в добычи сырья стала Австралия. Такие ведущие позиции сохранились вплоть до 1995 г. суммарно Северная Америка и Западная Европа добывают железной руды меньше, чем добывает одна Австралия.
Еще более существенные изменения произошли в добыче руды по странам. С каждым годом становится все более важным видом сырья – лом черных металлов. Лом черных металлов позволил экономить на производстве металлов. Так одна тонна лома позволяет экономить одну тонну чугуна и соответственно для его получения железную руду и кокс.
Металлофонд народного хозяйства развитых государств огромен и исчисляется сотнями миллионов и даже миллиардами тонн.
Основными его источниками стало являться вторсырье:
- амортизационный лом: идущие на слом машины, оборудование, здания и т.д.;
- производственный лом: отходы металлообработки;
- оборотный лом: отходы разливки стали.
Однако и здесь не обошлось без подводных камней. Формирование ресурсов лома (сбор, подготовка к переплаву) остается одной из главных проблем мировой металлургии. Мировой рынок лома определяется имеющимися ресурсами в зависимости от уровня развития хозяйства внутри каждой из стран, обладающей этим ресурсом. В целом ресурсы лома весьма велики, однако не одинаковы в отдельных странах.
В 1995 году потребность в ломе черных металлов достигала 385 млн. т. Около 40% стали было выплавлено во всех странах мира при использовании лома, как вторичного сырья. Существенно увеличивают спрос на него выгоды от переработки лома в электродуговых печах и в кислородных конвертерах. Относительно огромное количество лома участвует во внешней торговле: около 5-7 % образующихся ресурсов.
Производство металлургического кокса
Топливом и восстановителем железной руды при выплавке чугуна является получаемый из коксующихся углей кокс. Получают его коксохимические цехи в топливной или металлургической промышленности. Абсолютная роль кокса в мире так и не уменьшается несмотря на возникновение нового направления стали в бескоксовой (или бездоменной) металлургии. Лишенные ресурсов коксующихся углей страны вынуждены создавать его производство для своей металлургической промышленности, импортируя их в большом количестве. Уменьшились расходные нормы кокса на выплавку чугуна благодаря достижениям НТП. Таким образом, благодаря широкой модернизации отрасли наблюдается следующая динамика потребности производства в коксе: 1938 г. – средний в мире расход кокса на 1 т. чугуна составлял более 1,68 т., в 1960 г. он снизился до 1,09 т., а в 1990 г. сократился до 0,66 т. Уменьшить удельный расход сырья более чем в 2 раза позволило повышение качества железной руды, совершенствование технологии и техники выплавки чугуна.
Таким образом, начиная с 70-х годов XX века выжиг кокса в мире, несмотря на выплавку чугуна, стал примерно 350-360 млн. тонн в год. Многие страны мира, в особенности США и ряд стран Западной Европы, были вынуждены снизить уровень производства кокса в 2-3 раза. Таким образом, в период с 1938 по 1995 гг. размещение производства кокса существенно изменилось. Так Западная Европа до войны в 1938 г. была лидером по производству коксующегося угля, вырабатывая его более половины – 55%. В 50-х годах прошлого века мировое первенство перешло к богатой углем Северной Америке, там стало производиться более 40% кокса в мире. В 1990 г. лидерство по производству кокса перешло к Азии (43%), увеличив долю мирового производства кокса к 1995 г. до 55%.
Немаловажные сдвиги в роли продуцентов кокса произошли по отдельным странам: до Второй мировой войны выделялась Германия, после войны до 1961 г. — США, так как уровень промышленного производства, по отношению ко всем странам Европы и СССР, у страны было самым высоким. Затем, после укрепления СССР и вплоть до его распада в 1991 году, наша страна была крупнейшим производителем. После распада сверхдержавы, КНР с 1991 года является главным производителем.
Легирующие материалы необходимы для улучшения физических и химический свойств материала. В металлургической промышленности они являются необходимым звеном для получения: ферросплавов, низколегированных (содержащих до 2,5% легирующих металлов), среднелегированных (2,5-10%) и высоколегированных (свыше 10%) сталей. Конечно, в настоящее время использование легирующих материалов по сравнению с железом невелико. В основном это марганец, хром и никель, производящиеся, за год во всем мире в количестве не превышающем 1 млн. т. каждого.
Остальные металлы, относящиеся к этой подгруппе, используются намного реже, в большинстве своем годовое использование достигает где-то сотню килограммов. Поэтому существенное воздействие в металлургическом комплексе легирующие металлы не оказывают. Большинство государств являющимися лидерами по производству продукции черной металлургии не обеспечены всеми видами легирующих металлов, или, например, как Япония вообще не имеют их. В основном, легирующими материалами располагают в достаточном количестве лишь некоторыми из них следующие государства: Бразилия и Украина – марганцем, Россия и Канада – никелем, Бразилия и Индия – хромом, КНР – вольфрамом, США – молибденом.
Зависимость от импорта хрома, марганца и кобальта или сырья для их получения в Западной Европе составляет 100%, никеля 99, вольфрама 70%. В США она достигает 70% по никелю и вольфраму, по хрому 75, кобальту 95 и марганцу 100%. Основными экспортерами легирующих материалов являются – Россия, КНР, Африка, и Южная Америка. Эти страны имеют хорошую обеспеченность данной подгруппой материалов.
Производства металлургического комплекса.
В черной металлургии к основным производствам комплекса относится: полный цикл производства чугуна, стали и проката.
Получение металла в отрасли начинается с выплавки чугуна – сплава железа с углеродом. Так начинается первая стадия по производству металла. Около половины всей стали в мире производятся из выплавляемого в доменных печах чугуна. Выделим основные виды чугуна в зависимости от дальнейшего его использования:
- передельный (белый) чугун – данный вид чугуна в процессе получения стали проходит два основных этапа: из руды получают чугун, а затем его переплавляют в сталь. Свыше 85% приходится подавляющая часть производства чугуна;
- литейный (серый) чугун – с помощью этого вида чугуна изготавливаются всевозможные фасонные отливки.
Помимо «чистого» чугуна к продуктам доменного производства можно отнести и некоторые виды ферросплавов (например, ферросилиций, ферромарганец и др.). В металлургическом цикле доменный процесс является самым материалоемким в основном производстве. Для получения 1 тонны чугуна расходуется около 3 тонн железной руды, топлива, известняков, до 30 м^3 воды, кислорода и природного газа. Чтобы повысить эффективность чугунного производства – необходимо уменьшить количество расходов материалов и топлива. Однако это так и остается первоочередной проблемой применения высококачественной руды. Достигнуть определенного уровня экономического эффекта в современно производстве помогает также и увеличение объема доменных печей, что помогает уменьшить объемы инвестиций на сооружение домны, снизить себестоимость чугуна, улучшить технологический процесс, сократить расходы топлива.
Максимальные объемы домен за послевоенные годы выросли с 1500 до 5000 м^3. В настоящее время современная домна, максимального размера способна за один только год дать 4-4,5 млн. тонн чугуна, что равно выплавке чугуна в одной только Австрии или Мексике. Обострившиеся экономические и экологические проблемы потребовали качественные изменения в географии доменного производства. На сегодняшний день мы видим, что производство переместилось ближе к морскому побережью. Сдвиги производства произошли со стороны старопромышленных металлургических регионов в сторону развивающихся государств. В результате смещения границ производств в черной металлургии лидерами по производству чугуна на сегодняшний день являются Бразилия, Мексика, Аргентина, Южная Корея, Тайвань, Индия и Турция.
Так, наглядно можно увидеть следующие мировые тенденции по развитию стран-лидеров по выплавке чугуна:
1950 года:
США (59,4 млн.т.), СССР (19,2 млн.т.), Китай(12,6 млн.т.), Германия (11,2 млн.т.), Великобритания (9,8 млн.т.), Франция (7,7 млн.т.), Бельгия(3,7 млн.т.), Люксембург (2,5 млн.т.), Канада (2,2 млн.т.), Япония (млн.т.).
1970 года:
СССР (85,9 млн.т.), США (83,3 млн.т.), Япония (68,0 млн.т.), Германия (33,6 млн.т.), Франция (19,2 млн.т.), Великобритания (17,7 млн.т.), Китай (16,5 млн.т.), Бельгия (10,8 млн.т.), Италия (8,4 млн.т.), Канада (8,2 млн.т.)
На начало 1990-ч годов:
СССР (110,2 млн.т.), Япония (80,2 млн.т.), Китай (62,4 млн.т.), США (49,7 млн.т.), Германия (31,7 млн.т.), Бразилия (21,2млн.т.), Республика Корея (15,5 млн.т.), Франция(14,1 млн.т.), Великобритания (12,3 млн.т.), Индия (12,0 млн.т.);
На конец 2003 года:
Китай (202,3 млн.т.), Япония (82,1 млн.т.), Россия (48,3 млн.т.), США (39,0 млн.т.), Бразилия(32,0млн.т.), Германия (29,5 млн.т.), Украина (29,5 млн.т.), Республика Корея (27,3 млн.т.), Индия(26,6 млн.т.), Франция(13,0 млн.т.).
Из приведенных выше данных можно сделать следующие выводы:
На начало XXI века мировая промышленность по производству чугуна взяла основной вектор направления на добычу и производство чугуна в развивающихся странах. Все это обусловлена дешевой рабочей силой, ранее слабым освоением железной руды в данных экономических районов и обеднение месторождений сырья в старых металлургических районах.
В условиях НТР и НТП возник ряд крупных производств, основное производство которых нуждается в металле. Так в приведенных данных мы видим существенное увеличение по выплавке чугуна в мире.
Производство стали относится к промежуточной стадии металлургического цикла. Таким образом, сталь является полуфабрикатом, предназначенным для дальнейшего передела в прокат, идущего в другие отрасли хозяйства. Так, у каждого потребителя свои технические требования к качеству прокатных изделий из разных сортов стали. Принято различать сталь по следующим видам:
Обыкновенная сталь – по химическим свойствам относится к углеродистой (содержание углерода не более 0,6%), а по способу производства является сталью обыкновенного качества, выплавляется в мартеновских печах.
Качественная сталь – бывают легированными или углеродистыми. Широко востребованная в машиностроение и строительстве, обладает определенными физическими, химическими и механическими свойствами.
Высококачественная сталь – преимущественно выплавляются в электропечах или другими современными методами, гарантирующими высокую чистоту по неметаллическим включениям (содержание серы и фосфора менее 0,03%) и содержанию газов, а, следовательно, улучшение механических свойств.
По своим техническим свойствам сталь определяется содержанием в ней углерода и легирующих добавок:
- низкоуглеродистая;
- высокоуглеродистая.
Выпуск качественной стали непрерывно растет. Например, производство нержавеющей стали в период с 1960 по 1995 гг. возрос с 2 до 15 млн.т., т.е. производство возросло в 3,5 раза быстрее выплавки всей стали.
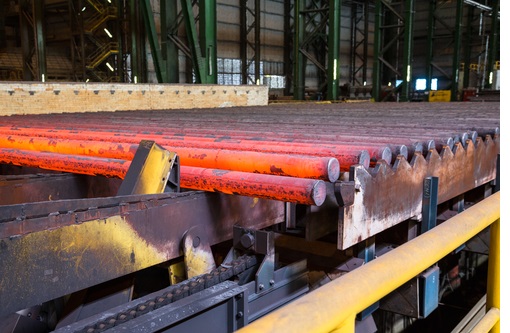
Бессемеровский и томасовский методы базировались на составе руд и получаемого из них чугуна для передела в сталь. Мартеновский метод был более универсальным, он позволял независимо от качества чугуна выплавлять сталь различного качества. К примеру, в году индустриализации в СССР этот метод был основным и до сих пор встречается на ряде российских предприятий.
В период НТР эффективными в сталеплавильном переделе оказались два процесса: кислородно-конвертерный и электросталеплавильный.
Кислородно-конвертерный способ предполагает получение стали из расплавленного чугуна и лома за 30-35 мин вместо 6-8 часов плавки в мартеновской печи. В дуговых электропечах – за 50-70 мин. Таким образом, благодаря процессу производства началось широкое и быстрое внедрение кислородно-конвертерного способа. Свой массовый масштаб способ производства охвати к 1997 г. – 60% в мире. Так, в настоящее время мартеновские печи дают в мире 7% стали, и они быстро выводятся из эксплуатации. Однако демонтаж мартеновских печей и сооружение кислородно-конвертерных цехов требует больших капитальных затрат. Поэтому техническое перевооружение промышленного производства металлургии даже в высокоразвитых странах длилась на протяжении четверти века: в 70-х годах прошлого века Япония перешла на конвертерный способ,
Великобритания и Франция – в 80-х годах, а США к началу 90-х готов. В России и Китае этот процесс перехода еще продолжается. В настоящее время, выплавка стали конвертерным способом происходит: в США – 61% от всей выплавляемой стали, во Франции – 64%, Японии – 68%, Великобритании – 74%, Германии – 76% и в Люксембурге – 100%.
Электросталеплавильный способ является вторым по значению процессе в производстве стали. Главным преимуществом этого метода является сравнительно небольшие затраты даже на крупные электродуговые печи, быстрый их ввод в строй, широкое использование лома. Сооружение миди - и минизаводов способствовало росту процессу получения электростали, что обусловило экономические выгоды от внедрения данного процесса. На сегодняшний день в мире доля электростали занимает 33%. Стоимость электростали оказывает большое влияние на развитие процесса. В относительно «молодых» странах черной металлургии – Тайвань, Бразилия, Республика Корея, на долю электростали приходится от 50% до 100% выплавки металла, а в остальных странах продуцентах стали (Западная Европа, США, Япония) от 24 до 40%. Исключение составляет Италия, она производит до 58% электростали.
Метод непрерывной разливки стали в сталеплавильном производстве приобрел особое значение, будучи экономически эффективным. Разработка и внедрение этого метода принадлежит СССР, где он получил широкое распространение внутри страны, а затем и в мире. Преимуществом метода является сокращение отходов производства на 20-30% уменьшая тем самым затраты на их переплавку. В 1995 году 76% всей произведенной стали в мире были произведены этим способом.
Получение стали из металлизированных окатышей, минуя выплавку чугуна – самая молодая технология в черной металлургии, но вместе с тем, она приобрела довольно весомое значение. Прямое восстановление железа (ПВЖ) во многом является процессом эффективным, как с экономической, так и с экологической стороны. Сегодня темп производства ПВЖ выше доменного. В связи с тем, что ПВЖ тяготеет к огромному количеству энергии (природный газ), то размещение его является целесообразным в странах и регионах богатых этим природным ресурсом. Таким образом, по этой технологии получения металла: на Азию приходится 40%, а Южную Америке 35%. На территории Северной Америки, Западной Европы и России существуют лишь отдельные опытные заводы.
Также как и распределение производства чугуна, мировая география стали терпит существенные изменения. В большинстве своем новые технологии используются малыми предприятиями в новых индустриальных странах. Основное месторасположение таких предприятий находится в промышленно малоосвоенных территориях, зачастую не располагающих первичным сырьем для производства. Мощный рост произошел в странах Восточной Европы и Азии. Суммарная доля в выплавки стали увеличилась с 22% до 55%. Однако темпы роста в получении стали были меньше, чем в освоении новых методик чугуна. Все это объясняется более меньшим спросом на сталь в связи с недостаточно развитым машиностроением в регионе.
Удельный вес выплавки стали в западных регионах снизился с 77 до 37%. В Южной Америке, Африке и в Австралии выплавка стали росла быстрее, чем чугуна. Большие сдвиги произошли в получении стали среди стран мира. Мы можем увидеть следующую тенденцию стран-лидеров по выплавке стали:
1950 гг.:
США (87,9 млн.т.), СССР (27,3 млн.т.), Великобритания (16,6 млн.т.), Германия (14,0 млн.т.), Франция (8,7 млн.т.), Япония (4,8 млн.т.), Бельгия (3,8 млн.т.), Канада (3,1 млн.т.), Люксембург (2,5 млн.т.), Италия (2,4 млн.т.);
1970 гг.:
США (119,3 млн.т.), СССР (115,9 млн.т.), Япония (93,3 млн.т.), Германия (45,0 млн.т.), Великобритания (28,5 млн.т.), Франция(23,3 млн.т.), Китай(18 млн.т.), Италия (17,3 млн.т.), Бельгия(12,6 млн.т.), Польша (11,8 млн.т.);
1990 гг.:
СССР(153,0 млн.т.), Япония (110,3 млн.т.), США (89,7 млн.т.), Китай (66,1 млн.т.), Германия (44,1 млн.т.), Италия(25,4 млн.т.), Республика Корея (23,1 млн.т.), Бразилия (20,6 млн.т.), Франция(19,3 млн.т.), Великобритания (17,9 млн.т.);
На начало 2003 года:
Китай (220,1 млн.т.), Япония (110,5 млн.т.), США (91,4 млн.т.), Россия (61,3 млн.т.), Республика Корея (46,3 млн.т.), Германия (44,9 млн.т.), Украина (36,7 млн.т.), Индия (31,8 млн.т.), Бразилия (31,1 млн.т.), Италия (26,7 млн.т.);
Таким образом, анализируя приведенные данные можно прийти к следующему выводу. В результате распада СССР, первенство в производстве стали формально перешли к Китаю, сместив страны СНГ. Однако если посчитать совокупную долю производства стали в странах СНГ можно заметить, что уровень производства стали снизился в бывших странах СССР незначительно. Во многом снижение производства произошло на территории современной Украины из-за тяжелой политической обстановки внутри страны.
Так же, мы видим, что страны с развивающейся экономикой начинают наращивать производство стали, смещая лидерство стран традиционно главенствующих в этой отрасли. Все это в первую обусловлено быстрым экономическим ростом стран, специализирующихся не на строительстве крупных промышленных центров, а отдельных мини - или мидизаводов, не требующих на свое создание вложения большим капитальных средств. Промышленность же старых районов производства стали в настоящее время проходит процесс реструктуризации, путем внедрения в производства нового оборудование. Процесс этот капиталоемкий, из-за чего старейшие производства вынуждены в период перехода к новым технологиям, уступать лидерство конкурентам.
Прокат представляет собой конечный продукт заключительной стадии всего производственного цикла черной металлургии. Стоимость проката в 2-5 раз больше стоимости стали. Прокат используется потребителями во всех отраслях народного хозяйства. Он является одним из востребованных товаров внешней торговли на рынке черного металла. Изделия из проката очень разнообразны, так их ассортимент в странах с развитой отраслью машиностроения достигает 20-30 тыс. видов. В настоящее время, в зависимости от спроса, ассортимент на изделия из проката продолжает обновляться.
Главными видами прокатного производства являются следующие товары:
- листовой металл (потребность в нем достигает 30-45% от всего проката в различных странах);
- сортовой металл (10-30% от общего числа прокатной продукции);
- заготовки для сварных труб и сами трубы (5-10%);
- катанка — горячекатаная проволока (3-8%);
- железнодорожный прокат (4-5%).
Прецизионный прокат в настоящее время приобрел исключительное значение для ряда машиностроительных отраслей. Отличается он высокой точностью размеров.
Крупным является и трубопрокатное производство, набравшее большой спрос на свою продукцию за счет развития трубопроводного транспорта.
Регионы черной металлургии
Во многих развитых странах после Второй мировой войны после восстановления и подъема отрасли последовали и глубокие спады в 70-80-х годах XX века. Подобные спады обусловлены нефтяным кризисом тех лет, следствием которого для металлургической промышленности явилось сокращение спроса на металл. Полностью прекратились из-за экономической нецелесообразности разработки месторождений бедных руд.
Старейший регион в металлургической промышленности мира – Западная Европа, остается одним из ведущих регионов по уровню развития отрасли. Широкая структурная перестройка черной металлургии началась в Западной Европе после того, как регион исчерпал свои ограниченные ресурсы сырья и отказался от добычи низкокачественных руд. Ведущие центры отрасли в Германии, Великобритании и Франции, помимо всех перечисленных проблем, испытывали тяжелую экологическую нагрузку, связанную с деятельностью металлургической промышленности. Таким образом, на сегодняшний день выплавка чугуна уменьшилась более чем вдвое – с 48% до 19%, стали – с 42 до 21%. Сильно сократилась добыча кокса в мире – с 55 до 11% в мире, а добыча железной руды в 10 раз.
В итоге структурных изменений сложилась новая специализация стран старого света — на получении качественных сталей (например, Западная Европа дает почти 1/2 нержавеющей стали) и изготовлении разнообразного, в том числе прецизионного, проката для мощного машиностроения.
Все приведенные события привели к изменению географии черной металлургии региона, отразившейся больше всего на крупных странах. Так Германия, будучи лидером в промышленности, уступила свое место Италии, не располагающей никакими видами сырья и топлива для получения металла. На сегодняшний день 2/5 выплавки чугуна и стали в старом свете приходятся на промышленные производства Италии и Германии.
На территории Северной Америки по-прежнему лидером в черной металлургии остается США. Обладая запасами значительных ресурсов железной руды, легирующих металлов и коксующихся углей, США не испытывает трудностей в отрасли, связанных с сырьевой базой производства. Кроме этого, ряд легирующих металлов ей поставляет Канада. Основной причиной устойчивого положения черной металлургии в стране, послужила хорошо развитая отрасль машиностроения, являющаяся главным потребителем металлов. Свои позиции по производству черных металлов США сохранило также благодаря использованию высоких достижений НТП, что помогло преодолеть ухудшение качества и уменьшение собственных ресурсов сырья, добиться эффективного использования импортной дальнепривозной железной руды.
В 1996 годах США переориентировалась на создание передельных мини - и мидизаводов в отрасли. На них было выплавлено свыше 42% стали в стране. В США полностью ликвидировали мартеновские производства благодаря новой технической и технологической политике. Процесс перехода, учитывая масштабы размеров металлургических предприятий в США, был дольше, чем в остальных странах. Страна стала меньше получать металла, однако, свое положение она компенсировала качеством.
На сегодняшний день бурное развитие отрасли черной металлургии произошли в ряде стран Азии и Южной Америки, ставших на путь быстрого индустриального развития. На сегодняшний день они превратились во влиятельных конкурентом США и Западной Европы.
По объемам получения главных видов продукции металлургической отрасли Азия превратилась в ведущий регион мира. Мощный прорыв в развитии черной металлургии совершили Япония, КНР, Республика Корея, Индия и о. Тайвань. На сегодняшний день КНР И Япония одни из крупней них производителей черных металлов в мире. Для черной металлургии в регионе имеются разнообразные виды сырья и топлива. Но степень обеспеченности ими неравномерна не только для отдельных стран, но и для всей Азии в целом. Имея крупными ресурсами коксующихся углей и рядом легирующих, КНР располагает рудами низкого качества. Япония практически не имеет металлургического сырья и топлива для обеспечения потребностей своей металлургии. Страны Азии могли бы компенсировать отсутствие своих ресурсов внутри региона, однако, объемы получения черных металлов настолько велики, что приходится закупить импорт. Большая роль первичной стадии цикла отводится в металлургии азиатского региона. Преобладает она в Китае и Индии. Япония, Республика Корея и о. Тайвань специализируются на производстве финальной стадии металлургии – выплавки стали и изготовления проката. Республика Корея по своему уровню развития отрасли превзошла целый ряд европейских стран, за исключением Германии.
Золотое время Восточной Европы пришлось на начало 60-х годов. Всего за десятилетний рубеж странам Восточной Европы по добыче сырья удалось оттеснить Северную Америку и Западную Европу. СССР вышло на первое место в мире по выплавке черных металлов. Экономическому и промышленному чуду в странах Восточной Европы способствовал ряд факторов: тесное экономическое сотрудничество со странами региона, значительный спрос на продукцию, полна обеспеченность региона сырьем и топливом. Однако за стремительным ростом последовало и падение, причиной которого стало моральное устарение процессов производств и распад СССР и следом за ним всего социалистического лагеря. После чего Западной Европе и США удалось вновь установить свое господство в отрасли.
Внешняя торговля товарами черной металлургии
На самом деле экспорт продукции черной металлургии довольно мал – около 3%, главным образом из-за невысокого уровня цен на ее товары. В основном на экспорт идет сырье и прокат. Спрос на промежуточные продукты мал. Так на 1995 г. экспорт составил 45% от всей добываемой руды в мире, проката – 20%, чугуна – менее 2%.
Бразилия и Австралия являются мировыми лидерами по экспорту железной руды – 65%.
На начало 2000-х годов сложился широкий межстрановой (чаще внутрирегиональный) торговый обмен прокатом разных видов. Основными потребителями проката являются Азия (в особенности Китай) и США. Главными поставщиками для них являются Западная и Восточная Европа.