Сплавы кальция
Технология получения сплавов, содержащих кальций, и его свойства
Кальций принадлежит к щелочноземельным металлам и располагается во II группе, в главной подгруппе А периодической таблицы. Его содержание в земле оценивается в 3,6 %. Наличие положительной валентности, обусловленной наличием двух свободных электронов, предопределяет высокую агрессивность элемента. Его физико-химические свойства следующие:
• атомный вес - 40,08;
• плотность - 1,54 г/см3;
• температура плавления - 810 °С;
• Температура кипения - 1439 °С.
При взаимодействии с кислородом кальций образует исключительно устойчивое вещество ─ оксид кальция (CaO). Его теплота образования 626 кДж/моль или 151780 кал/мол. Плавится оксид при 2587 °С, кипит 3627 °С.
Реакция кальция с углеродом дает прочный карбид (CaC2), плавящийся при 2300 °С. Известны три соединения Са с кремнием ─ силициды (Ca2Si, CaSi, CaSi2). С железом кальций взаимно нерастворим. В жидкой фазе кальций образует с кремнием непрерывный ряд растворов. Их сплавы, маркируемые СК25 и СК30, а также тройные сплавы СК10 и СК15 применяются как раскислители сталей, для получения сложных сплавов и добавок.
Физико-химические основы получения силикокальция
Для производства силикокальция необходимы кварцит и восстановитель. Требования к ним такие же, как при выплавке ферросилиция. Получение силикокальция происходит с помощью восстановления кремнезема (SiO2) и оксида кальция (CaO) углеродом.
Восстановление беспримесной окиси кальция следует уравнению (СаО) + 3Ст=[СаС2] + {CO}. Реакция начинается при температуре 1765 °С. По указанной реакции получается карбид кальция. При совместном восстановлении карбида кальция и кремнезема протекает реакция 2(SiО2) + (CaO) + 5Ст = [СаSi2] + 5{CO}, на финише получается силицид кальция [СаSi2]. Для реакции смесь необходимо нагреть до 1580 °С, что ниже температуры восстановления окислов по отдельности.
Параллельно происходит шлакообразование. Для него нужны температуры ниже начала отмеченных выше реакций, поэтому шлаки появляются раньше. Исходные продукты в печи восстанавливаются углеродом, а также кремнием и его карбидом.
При методе углетермии для получения силикокальция СК25 и СК15 кальций и кремний в присутствии железа восстанавливаются проще. Силициды кальция растворяются в нем, выходят из зон реакции, что благоприятно для реакций восстановления. Известь выгоднее восстанавливать в присутствии кремния, тогда не образовываются карбиды. Процесс описывается реакцией 2(СаО) + 3[Si] = 2[СаSi] + (SiО2).
Технология производства силикокальция
Для выплавки марок СК25 и СК30 используются электропечи, выложенные внутри углем. Их мощность 10 ─ 15 мегавольт-ампер (МВ-A). При подаваемом напряжении 120 ─ 140 вольт по электродам течет ток 50 ─ 55 килоампер (кА). В результате электроды устойчиво держатся в шихте, проникая на глубину 50 см. Ванна в печи делает оборот за трое суток. При таких параметрах карбиды разрушаются, и силикокальций выплавляется циклами по 10 ─ 13 недель.
Карбиды и шлаки образуют застывшие остатки продукта (козел). Для очистки печи от этих остатков, ее 1 ─ 1,5 месяца используют для выплавки сорока пяти процентного ферросилиция, после чего печь 2,5 ─ 3 месяца будет снова пригодна для производства силикокальция.
Карбиды при этом процессе покрывают ванну, поэтому каждые полтора года необходима замена футеровки. После капремонта в печи месяц выплавляют ферросплав с 45 % кремния. Для этого готовят смесь (шихту), содержащую 67 % кальция и 75 % кремния. Для первого цикла выплавок твердого углерода надо добавлять с избытком 10 ─ 12 %, для второй, когда козел будет разрушен 15 ─ 16 %.
В порции шихты должны содержаться:
• Кварцит 200 кг;
• Оксид кальция 85 кг;
• Древесный уголь 50 кг;
• Каменный уголь 30 кг;
• Коксик 100 кг.
Силикокальций выплавляется непрерывным методом, рабочую смесь добавляют в печь после проплавления предыдущей партии. Необходимая энергия для шихты с 0,2 т кварцита (столько входит в устройства для подачи сырья ─ колоша, она представляет собой конус) составляет 1640 ─ 1700 квт-ч.
Для хорошего функционирования электропечи к электродам постоянно подгребают карборунд (сплавленный диоксид кремния с углем). Он спекается и осаждается на поверхности колошника. Карборунд надо каждую смену удалять. Восстановительные реакции активно идут в горячих зонах возле электродов. Вокруг них возникают газовые полости, их нижняя часть выстлана карбидом (чашки). Получаемый расплав собирается в полости, расположенной в плоскости выпускного отверстия. Чтобы процессы шли штатно, необходимо сохранять чашки и не допускать исчезновения полости.
Для этого нужен излишний восстановитель, но избыточное образование карбидов перекроит полость, и расплав, шлаки, газ не смогут выходить из летка (отверстие для выпуска). Во избежание этого добавляют 0,4 ─ 0,6 кварцита на плавку. Его помещают около электрода, подгребают горячую шихту, сверху засыпают новую шихту обычной температуры. При правильной работе в печи образуется минимум шлака, состоящего из диоксида кремния (≈ 50 %), окиси кальция (15 ─ 20 %), SiC (10 %), CaC2 (10 ─ 20 %), около 3 % окиси алюминия, остальное приходится на магний, окись железа и прочее. Силикокальций выпускают в ковш, обложенный графитовой плиткой, после чего разливают в изложницу из чугуна.
Производство силикокальция марок СК10 и СК15
Силикокальций получают в печи закрытого типа мощностью 3,5 мегавольт-ампер с вращающейся ванной. Футеровка сделана из угля, напряжение подается 127 В. Для расчета состава и количества шихты за основу берется необходимое количество кремния, содержащегося в ферросилиции.
1. На восстановление потребуется 15 % требуемого Si.
2. В выплавляемый сплав перейдет 55 %.
3. При взаимодействии с воздухом окислится 20 %.
4. Прореагирует с железными стержнями, служащими для перемешивания расплава 10 %.
Известь берется с избытком, составляющим 10 %, потребуется 15 кг плавикового шпата на 0,1 т ферросилиция. Расчетным путем определяется состав колоши. 0,2 т извести,
198 кг ферросилиция, необходимо добавить 30 кг плавикового шпата. Лучшая пропорция для смеси оксида кальция и свободного кремния лежит в диапазоне 1,7 ─ 2.
Значения больше двух повлекут увеличенное содержание в конечном продукте кальция за счет снижения концентрации железа. Сплав окажется с меньшим удельным весом, электродуга опустится, будет гореть прямо на сплаве, что вызовет большие потери кальция и кремния, ухудшится эффективность работы печи, уменьшится разделение сплава и шлака, как следствие повышенный брак конечной продукции, загрязненной шлаками.
Плавиковый шпат уменьшает удельный вес шлака за счет увеличения пористости, оптимизирует отделение сплава от шлака, положительно влияет на снижение угара и невозвратные потери конечного металла.
Процесс плавки носит циклический характер, требующий полного проплавления сырьевой смеси. За время плавки, 2 часа, подают 12 партий шихты. На одну колошу шихты потребуется 380 ─ 420 квт-ч. электрической энергии. Нормально работающая печь поддерживает стабильное энергопотребление и выплавляет металл с устойчивой концентрацией кальция 16 ─ 19 %. Шлак вытекает из электропечи планомерно и охлаждаясь, рассыпается.
Уменьшение концентрации кальция в сплаве связано с избыточным количеством ферросилиция в шихте или недостатком окиси кальция в извести. Повышенное содержание Са в металле объясняется нехваткой восстановителя. Вследствие этого сужается зона расплавления, часть сплава всплывает поверх шлака, что приводит к снижению выхода готового металла.
Сплаву и шлаку дают вытечь из печи в одно и то же время четырежды за смену в ковш, выстеленной графитовой плиткой с теплоизолирующим слоем из шамота. После аккуратного удаления шлака, расплавленный металл разливают в изложницы из чугуна. Когда металл охладится, его дробят, чистят и упаковывают в стальные барабаны.
В шлаке присутствуют оксид кальция (62 ─ 68 %), диоксид кремния (30 ─ 33), отдельно застывшие шарики металла (2 ─ 5 %). Выплавляют силикокальций с 15 % Са в печи открытого типа мощностью 15 МВ-А углетермическим методом. Загружаемое за один раз количество шихты содержит 220 кг кварцита, 85 кг мелкодисперсного кокса, по 50 и 30 кг древесного и каменного угля соответственно, 55 кг железной стружки. Плавку осуществляют непрерывным процессом.
Во время разливки ферросилиция возникают определенные сложности в эксплуатации летки. Это связано с повышенным выходом расплавленного шлака. В сплаве находится повышенная концентрация алюминия (≈ 1 %) и углерода, наблюдается большое количество шлаковых включений. Примерный их состав - 1/5 диоксид кремния, половина окись кальция и 1/3 карбид кальция.
Многостадийность технологии, недостаточно конкурентные общие технико-экономические показатели вызывают непреодолимые проблемы с приемлемой рентабельностью данного производства. Сплав аналогичного состава можно производить намного технологичней и с меньшими затратами методом смешения непосредственно в ковше расплавленного силикокальция и ферросилиция, содержащего 18 % кремния.
Кальций принадлежит к щелочноземельным металлам и располагается во II группе, в главной подгруппе А периодической таблицы. Его содержание в земле оценивается в 3,6 %. Наличие положительной валентности, обусловленной наличием двух свободных электронов, предопределяет высокую агрессивность элемента. Его физико-химические свойства следующие:
• атомный вес - 40,08;
• плотность - 1,54 г/см3;
• температура плавления - 810 °С;
• Температура кипения - 1439 °С.
При взаимодействии с кислородом кальций образует исключительно устойчивое вещество ─ оксид кальция (CaO). Его теплота образования 626 кДж/моль или 151780 кал/мол. Плавится оксид при 2587 °С, кипит 3627 °С.
Реакция кальция с углеродом дает прочный карбид (CaC2), плавящийся при 2300 °С. Известны три соединения Са с кремнием ─ силициды (Ca2Si, CaSi, CaSi2). С железом кальций взаимно нерастворим. В жидкой фазе кальций образует с кремнием непрерывный ряд растворов. Их сплавы, маркируемые СК25 и СК30, а также тройные сплавы СК10 и СК15 применяются как раскислители сталей, для получения сложных сплавов и добавок.
Физико-химические основы получения силикокальция
Для производства силикокальция необходимы кварцит и восстановитель. Требования к ним такие же, как при выплавке ферросилиция. Получение силикокальция происходит с помощью восстановления кремнезема (SiO2) и оксида кальция (CaO) углеродом.
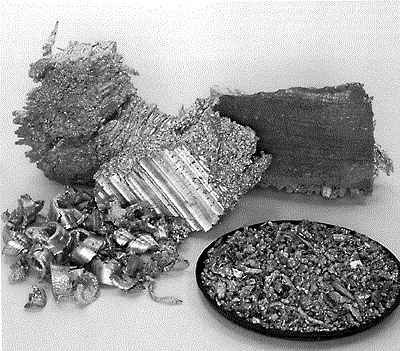
Параллельно происходит шлакообразование. Для него нужны температуры ниже начала отмеченных выше реакций, поэтому шлаки появляются раньше. Исходные продукты в печи восстанавливаются углеродом, а также кремнием и его карбидом.
При методе углетермии для получения силикокальция СК25 и СК15 кальций и кремний в присутствии железа восстанавливаются проще. Силициды кальция растворяются в нем, выходят из зон реакции, что благоприятно для реакций восстановления. Известь выгоднее восстанавливать в присутствии кремния, тогда не образовываются карбиды. Процесс описывается реакцией 2(СаО) + 3[Si] = 2[СаSi] + (SiО2).
Технология производства силикокальция
Для выплавки марок СК25 и СК30 используются электропечи, выложенные внутри углем. Их мощность 10 ─ 15 мегавольт-ампер (МВ-A). При подаваемом напряжении 120 ─ 140 вольт по электродам течет ток 50 ─ 55 килоампер (кА). В результате электроды устойчиво держатся в шихте, проникая на глубину 50 см. Ванна в печи делает оборот за трое суток. При таких параметрах карбиды разрушаются, и силикокальций выплавляется циклами по 10 ─ 13 недель.
Карбиды и шлаки образуют застывшие остатки продукта (козел). Для очистки печи от этих остатков, ее 1 ─ 1,5 месяца используют для выплавки сорока пяти процентного ферросилиция, после чего печь 2,5 ─ 3 месяца будет снова пригодна для производства силикокальция.
Карбиды при этом процессе покрывают ванну, поэтому каждые полтора года необходима замена футеровки. После капремонта в печи месяц выплавляют ферросплав с 45 % кремния. Для этого готовят смесь (шихту), содержащую 67 % кальция и 75 % кремния. Для первого цикла выплавок твердого углерода надо добавлять с избытком 10 ─ 12 %, для второй, когда козел будет разрушен 15 ─ 16 %.
В порции шихты должны содержаться:
• Кварцит 200 кг;
• Оксид кальция 85 кг;
• Древесный уголь 50 кг;
• Каменный уголь 30 кг;
• Коксик 100 кг.
Силикокальций выплавляется непрерывным методом, рабочую смесь добавляют в печь после проплавления предыдущей партии. Необходимая энергия для шихты с 0,2 т кварцита (столько входит в устройства для подачи сырья ─ колоша, она представляет собой конус) составляет 1640 ─ 1700 квт-ч.
Для хорошего функционирования электропечи к электродам постоянно подгребают карборунд (сплавленный диоксид кремния с углем). Он спекается и осаждается на поверхности колошника. Карборунд надо каждую смену удалять. Восстановительные реакции активно идут в горячих зонах возле электродов. Вокруг них возникают газовые полости, их нижняя часть выстлана карбидом (чашки). Получаемый расплав собирается в полости, расположенной в плоскости выпускного отверстия. Чтобы процессы шли штатно, необходимо сохранять чашки и не допускать исчезновения полости.
Для этого нужен излишний восстановитель, но избыточное образование карбидов перекроит полость, и расплав, шлаки, газ не смогут выходить из летка (отверстие для выпуска). Во избежание этого добавляют 0,4 ─ 0,6 кварцита на плавку. Его помещают около электрода, подгребают горячую шихту, сверху засыпают новую шихту обычной температуры. При правильной работе в печи образуется минимум шлака, состоящего из диоксида кремния (≈ 50 %), окиси кальция (15 ─ 20 %), SiC (10 %), CaC2 (10 ─ 20 %), около 3 % окиси алюминия, остальное приходится на магний, окись железа и прочее. Силикокальций выпускают в ковш, обложенный графитовой плиткой, после чего разливают в изложницу из чугуна.
Производство силикокальция марок СК10 и СК15
Силикокальций получают в печи закрытого типа мощностью 3,5 мегавольт-ампер с вращающейся ванной. Футеровка сделана из угля, напряжение подается 127 В. Для расчета состава и количества шихты за основу берется необходимое количество кремния, содержащегося в ферросилиции.
1. На восстановление потребуется 15 % требуемого Si.
2. В выплавляемый сплав перейдет 55 %.
3. При взаимодействии с воздухом окислится 20 %.
4. Прореагирует с железными стержнями, служащими для перемешивания расплава 10 %.
Известь берется с избытком, составляющим 10 %, потребуется 15 кг плавикового шпата на 0,1 т ферросилиция. Расчетным путем определяется состав колоши. 0,2 т извести,
198 кг ферросилиция, необходимо добавить 30 кг плавикового шпата. Лучшая пропорция для смеси оксида кальция и свободного кремния лежит в диапазоне 1,7 ─ 2.
Значения больше двух повлекут увеличенное содержание в конечном продукте кальция за счет снижения концентрации железа. Сплав окажется с меньшим удельным весом, электродуга опустится, будет гореть прямо на сплаве, что вызовет большие потери кальция и кремния, ухудшится эффективность работы печи, уменьшится разделение сплава и шлака, как следствие повышенный брак конечной продукции, загрязненной шлаками.
Плавиковый шпат уменьшает удельный вес шлака за счет увеличения пористости, оптимизирует отделение сплава от шлака, положительно влияет на снижение угара и невозвратные потери конечного металла.
Процесс плавки носит циклический характер, требующий полного проплавления сырьевой смеси. За время плавки, 2 часа, подают 12 партий шихты. На одну колошу шихты потребуется 380 ─ 420 квт-ч. электрической энергии. Нормально работающая печь поддерживает стабильное энергопотребление и выплавляет металл с устойчивой концентрацией кальция 16 ─ 19 %. Шлак вытекает из электропечи планомерно и охлаждаясь, рассыпается.
Уменьшение концентрации кальция в сплаве связано с избыточным количеством ферросилиция в шихте или недостатком окиси кальция в извести. Повышенное содержание Са в металле объясняется нехваткой восстановителя. Вследствие этого сужается зона расплавления, часть сплава всплывает поверх шлака, что приводит к снижению выхода готового металла.
Сплаву и шлаку дают вытечь из печи в одно и то же время четырежды за смену в ковш, выстеленной графитовой плиткой с теплоизолирующим слоем из шамота. После аккуратного удаления шлака, расплавленный металл разливают в изложницы из чугуна. Когда металл охладится, его дробят, чистят и упаковывают в стальные барабаны.
В шлаке присутствуют оксид кальция (62 ─ 68 %), диоксид кремния (30 ─ 33), отдельно застывшие шарики металла (2 ─ 5 %). Выплавляют силикокальций с 15 % Са в печи открытого типа мощностью 15 МВ-А углетермическим методом. Загружаемое за один раз количество шихты содержит 220 кг кварцита, 85 кг мелкодисперсного кокса, по 50 и 30 кг древесного и каменного угля соответственно, 55 кг железной стружки. Плавку осуществляют непрерывным процессом.
Во время разливки ферросилиция возникают определенные сложности в эксплуатации летки. Это связано с повышенным выходом расплавленного шлака. В сплаве находится повышенная концентрация алюминия (≈ 1 %) и углерода, наблюдается большое количество шлаковых включений. Примерный их состав - 1/5 диоксид кремния, половина окись кальция и 1/3 карбид кальция.
Многостадийность технологии, недостаточно конкурентные общие технико-экономические показатели вызывают непреодолимые проблемы с приемлемой рентабельностью данного производства. Сплав аналогичного состава можно производить намного технологичней и с меньшими затратами методом смешения непосредственно в ковше расплавленного силикокальция и ферросилиция, содержащего 18 % кремния.