Технология изготовления ферротитана FeTi
Чаще всего ферротитан производят посредством алюмотермического метода.
Для того чтобы восстановить главные окислы концентрата титана алюминием, используют специальные реакции.
Корректное выполнение алюмотермического процесса изготовления ферротитана осуществляется поддержанием удельной теплоты на уровне 2,55 – 2,60 мДж/кг, т.е. 610 – 620 килокалорий/кг. Чтобы этого достичь, в плавильную печь добавляют шихту с определенным составом, нагревая ее, что приводит к увеличению удельной теплоты примерно на 125,6 кДж/кг, т.е. 30 килокалорий/кг, через каждые 100 градусов подогрева.
В ходе изготовления ферротитана, титан смешивается с железом, затем в процессе возникает сплав титана с алюминием и кремнием, что улучшает химическое взаимодействие во время восстановления и ускоряет создание титанового сплава. Прирост доли титана в сплаве ведет к повышению доли алюминия в шихте, что в свою очередь ведет к повышению объема алюминия в сплаве.
Из-за того, что возникает прочный силицид титана Ti5Si3, стремятся увеличить количество извлекаемого титана и понизить остаточную долю алюминия в сплаве посредством добавления в шихту ферросилиция ФС45 или ФС75 в случае увеличения части кремния в ферросплаве до 5 – 5,5 %.
Оксид титана, будучи достаточно сильной основой, в состоянии соединиться с глиноземом, что уменьшает количество титана. Для того чтобы не допустить этого, в процессе создания ферротитана в шихту добавляют СаО – это позволяет восполнить часть TiO, соединившегося с глиноземом. Такой шаг дает возможность увеличить уровень восстановления титана, но это ведет к уменьшению температуры, что в свою очередь повышает количество утрачиваемых корольков в шлаке. Нормальный объем извести – приблизительно 1/5 часть от массы алюминия.
Состав шихты, необходимой для изготовления ферротитана, формируют исходя из того, что в готовый сплав из нее попадет в процентном соотношении от изначального количества: титана – 77, кремния – 90, марганца – 90, железа – 99, серы – 70. Соответственно в шлаке останется 23 % титана (по 11,5 % TiO и Ti2O3), десятая часть кремния, весь объем цинка, а 1/3 серы уходит в улет.
Для сплавления ферротитана температура в печи должна составлять 1950 °С. При этом энергозатраты распределяются так: 29,2 % тепла нужно на нагрев сплава, 52,5 % уходит на прогрев шлака, а 18,2 % энергии составляют потери.
Все ингредиенты для шихты в нужных пропорциях соединяют и помещают в бункер для плавления, а оттуда смесь отправляется в шахту для плавки винтовым питателем.
В конструкцию шахты для плавки входит разборная чугунная шахта цилиндрической формы, которая закреплена на зафутерованной огнеустойчивой кирпичной тележке. На ней в итоге проводится наплавка постоянной подины из 10 – 15 -процентного ферротитана. Доля концентрата в шихтовой колоше составляет 100 кг, порошкообразного алюминия - 42,5 –45,4 кг, извести – 10,5 кг, 75-процентного ферросилиция – 0,95 – 1,85 кг. Разовый цикл плавки ферросплава включает 38 колош. Изготовление ферротитана осуществляется посредством нижнего запала. На подовую плиту выгружают шихту массой 50 кг, которая подвергается поджогу электрическим запалом. Обычно плавка длится 15 – 18 минут - при 4 т концентрата. Цикл плавки может замедляться по причине уменьшения удельной теплоты процесса или наличием изъяна в восстановителе. Интенсивно протекающая плавка зачастую возникает из-за наличия чрезмерного содержания влаги в шихте или футеровке.
После окончания процесса плавки сверху на расплав добавляют смесь железа с термитом (0,3 т железной руды, 56 – 67 кг порошкообразного алюминия, 18 – 20 кг ферросилиция и 100 кг извести). Это дает возможность шлаку раствориться, а королькам предоставляется возможность оседания, что улучшает показатели входа титана в сплав по завершении процесса. Для удачного оседания корольков используют электрический подогрев шлака.
Плавка с высокой результативностью осуществляется посредством разливки ферротитана из наклоняющегося ковша. В таком случае непосредственно по завершении плавки проводят разливку по изложницам с основаниями из блока, имеющего малый процент ферротитана. В первую очередь сливают 0,3 -метровый слой шлака и ждут 1,5 минуты, пока не образуется гарнисаж из шлака требуемой толщины, после чего сливают оставшийся расплав.
Если применять шихту из отходов металлического титана, то их потребуется нагреть до 300 – 400 °С и загрузить под запальное вещество в таком просчете, чтобы образовывающийся шлак во время проплавления перекрывал их и препятствовал контакту с воздухом. Переплав отработанного титана дает возможность увеличить объем титана в ферросплаве до 35 – 40 %, уменьшить долю алюминия приблизительно на 50 – 80 кг и концентрата приблизительно на 100 – 200 кг на каждую тонну сплава.
По завершении затвердевания блока, сплав подвергается очистке от шлака и охлаждению при помощи воды, после чего разделяют сплав. Шлаки алюмотермического изготовления ферротитана, как правило, включают: 11,7 – 13,3 % оксида титана; до 0,5 % диоксида кремния; 10 – 14 % оксида кальция; 3 – 4 % оксида магния; 0,8 – 2 % оксида железа и 70 – 74 % оксида алюминия. Соотношение масс шлака и металла - 1,3.
Чтобы изготовить одну тонну 20-процентного ферротитана требуется 0,98 т ильменитового концентрата (42 % TiO2),
0,42 т алюминия, 70 кг железной руды, 50 кг отработанного титана и 100 кг извести. Учитывая ожидаемые потери во время обжига, полезный выход титана равняется 68 процентам.
Согласно методу Ключевского завода ферросплавов, можно произвести ферротитан с содержанием титана от 37,5 до 40 %, используя двухстадийную плавку в электропечи с предшествующим расплавлением перовскитового концентрата (половина от всего объема концентратов титана) и будущей проплавкой ильменитового концентрата с алюминием в момент, когда печь находится в выключенном состоянии. Для 1 тонны сплава в таком случае потребуется 0,38 т порошка алюминия, при этом становится возможным извлечь титан на 71 %.
Разновидности сплавов FeTi
В чистом виде у титана удельная плотность составляет 4,5 г/см3, плавится он при 1670 °С, а закипает при 3170 °С.
При сплавлении его с углеродом выходит прочный карбид TiC с температурой плавления 3177 °С. Соединение с кремнием дает несколько видов сплавов – силициды (сплавы кремния с менее электроотрицательными металлами) Ti5Si3, TiSi и TiSi2, а также весьма плотный сплав Ti6Si3, который плавится при 2120 °С. При сплавлении титана с алюминием на выходе получаются соединения TiAl иTiAl3.
Связываясь с кислородом, титан образует несколько видов окислов – двуокись TiO2 (плавится при 1950 °С), оксид TiO (плавление при 2020 °С), и окись Ti2O3 (температура плавления 2130 °С).
Соединение железа с титаном дает на выходе два вида сплавов – TiFe (Тпл = 1317 °С) и TiFe2 (Тпл = 1427 °С). Полный состав ферротитана можно узнать из таблицы.
Ферротитан получают, главным образом, из концентратов минеральных пород, таких как ильмениты (FeOTiO2). Кроме того, титан содержится в таких минералах, как рутил TiO2, ксантитан TiO2(Al2O3)nH2O, перовскит CaOTiO2.
Состав концентрата 1 сорта включает: TiO2 – не меньше 42 %, Fe2O3 – не более 53,6 %, SiO2 – менее 2,5 %, P – не больше 0,025 %, и не более 7 % H2O. Сырье проходит предварительный окислительный обжиг, температура в печи во время процесса составляет 1100 – 1150 °С. Делается это чтобы снизить уровень серы до 0,04 %, а также для получения оксида железа при расплавлении ильменита. Такая обработка дает возможность увеличить количество используемого при плавлении титана, уменьшить потребление алюминия, а также повысить температуру процесса.
Отходы металлического титана тоже могут быть использованы для изготовления ферротитана, однако для этого они должны быть абсолютно сухими. Кроме того, подходит и титановая стружка. Для целей производства стружку прессуют в брикеты или пакетируют в железную тару.
Восстанавливают титан из отходов с помощью порошка ФС75 и крупки из вторичного алюминия. Для получения крупки алюминий в жидком состоянии распыляют сжатым воздухом или азотом, который пропускают сквозь узкую форсунку. Молотая известь с зерном менее 3 мм служит флюсом, она содержит менее 1 % углерода и более 90 % CaO.
Малофосфористая гематитовая руда (Fe2O3 – 97 %, P – менее 0,015 %), измельченная до размеров зерна в 3 мм, применяется в железотермитном осадителе. Чтобы удалить влагу, руду предварительно просушивают.
Для того чтобы восстановить главные окислы концентрата титана алюминием, используют специальные реакции.
Корректное выполнение алюмотермического процесса изготовления ферротитана осуществляется поддержанием удельной теплоты на уровне 2,55 – 2,60 мДж/кг, т.е. 610 – 620 килокалорий/кг. Чтобы этого достичь, в плавильную печь добавляют шихту с определенным составом, нагревая ее, что приводит к увеличению удельной теплоты примерно на 125,6 кДж/кг, т.е. 30 килокалорий/кг, через каждые 100 градусов подогрева.
В ходе изготовления ферротитана, титан смешивается с железом, затем в процессе возникает сплав титана с алюминием и кремнием, что улучшает химическое взаимодействие во время восстановления и ускоряет создание титанового сплава. Прирост доли титана в сплаве ведет к повышению доли алюминия в шихте, что в свою очередь ведет к повышению объема алюминия в сплаве.
Из-за того, что возникает прочный силицид титана Ti5Si3, стремятся увеличить количество извлекаемого титана и понизить остаточную долю алюминия в сплаве посредством добавления в шихту ферросилиция ФС45 или ФС75 в случае увеличения части кремния в ферросплаве до 5 – 5,5 %.
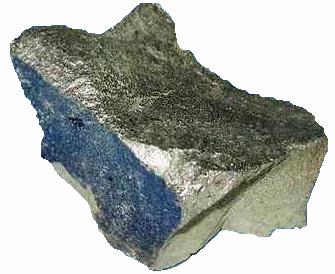
Состав шихты, необходимой для изготовления ферротитана, формируют исходя из того, что в готовый сплав из нее попадет в процентном соотношении от изначального количества: титана – 77, кремния – 90, марганца – 90, железа – 99, серы – 70. Соответственно в шлаке останется 23 % титана (по 11,5 % TiO и Ti2O3), десятая часть кремния, весь объем цинка, а 1/3 серы уходит в улет.
Для сплавления ферротитана температура в печи должна составлять 1950 °С. При этом энергозатраты распределяются так: 29,2 % тепла нужно на нагрев сплава, 52,5 % уходит на прогрев шлака, а 18,2 % энергии составляют потери.
Все ингредиенты для шихты в нужных пропорциях соединяют и помещают в бункер для плавления, а оттуда смесь отправляется в шахту для плавки винтовым питателем.
В конструкцию шахты для плавки входит разборная чугунная шахта цилиндрической формы, которая закреплена на зафутерованной огнеустойчивой кирпичной тележке. На ней в итоге проводится наплавка постоянной подины из 10 – 15 -процентного ферротитана. Доля концентрата в шихтовой колоше составляет 100 кг, порошкообразного алюминия - 42,5 –45,4 кг, извести – 10,5 кг, 75-процентного ферросилиция – 0,95 – 1,85 кг. Разовый цикл плавки ферросплава включает 38 колош. Изготовление ферротитана осуществляется посредством нижнего запала. На подовую плиту выгружают шихту массой 50 кг, которая подвергается поджогу электрическим запалом. Обычно плавка длится 15 – 18 минут - при 4 т концентрата. Цикл плавки может замедляться по причине уменьшения удельной теплоты процесса или наличием изъяна в восстановителе. Интенсивно протекающая плавка зачастую возникает из-за наличия чрезмерного содержания влаги в шихте или футеровке.
После окончания процесса плавки сверху на расплав добавляют смесь железа с термитом (0,3 т железной руды, 56 – 67 кг порошкообразного алюминия, 18 – 20 кг ферросилиция и 100 кг извести). Это дает возможность шлаку раствориться, а королькам предоставляется возможность оседания, что улучшает показатели входа титана в сплав по завершении процесса. Для удачного оседания корольков используют электрический подогрев шлака.
Плавка с высокой результативностью осуществляется посредством разливки ферротитана из наклоняющегося ковша. В таком случае непосредственно по завершении плавки проводят разливку по изложницам с основаниями из блока, имеющего малый процент ферротитана. В первую очередь сливают 0,3 -метровый слой шлака и ждут 1,5 минуты, пока не образуется гарнисаж из шлака требуемой толщины, после чего сливают оставшийся расплав.
Если применять шихту из отходов металлического титана, то их потребуется нагреть до 300 – 400 °С и загрузить под запальное вещество в таком просчете, чтобы образовывающийся шлак во время проплавления перекрывал их и препятствовал контакту с воздухом. Переплав отработанного титана дает возможность увеличить объем титана в ферросплаве до 35 – 40 %, уменьшить долю алюминия приблизительно на 50 – 80 кг и концентрата приблизительно на 100 – 200 кг на каждую тонну сплава.
По завершении затвердевания блока, сплав подвергается очистке от шлака и охлаждению при помощи воды, после чего разделяют сплав. Шлаки алюмотермического изготовления ферротитана, как правило, включают: 11,7 – 13,3 % оксида титана; до 0,5 % диоксида кремния; 10 – 14 % оксида кальция; 3 – 4 % оксида магния; 0,8 – 2 % оксида железа и 70 – 74 % оксида алюминия. Соотношение масс шлака и металла - 1,3.
Чтобы изготовить одну тонну 20-процентного ферротитана требуется 0,98 т ильменитового концентрата (42 % TiO2),
0,42 т алюминия, 70 кг железной руды, 50 кг отработанного титана и 100 кг извести. Учитывая ожидаемые потери во время обжига, полезный выход титана равняется 68 процентам.
Согласно методу Ключевского завода ферросплавов, можно произвести ферротитан с содержанием титана от 37,5 до 40 %, используя двухстадийную плавку в электропечи с предшествующим расплавлением перовскитового концентрата (половина от всего объема концентратов титана) и будущей проплавкой ильменитового концентрата с алюминием в момент, когда печь находится в выключенном состоянии. Для 1 тонны сплава в таком случае потребуется 0,38 т порошка алюминия, при этом становится возможным извлечь титан на 71 %.
Разновидности сплавов FeTi
В чистом виде у титана удельная плотность составляет 4,5 г/см3, плавится он при 1670 °С, а закипает при 3170 °С.
При сплавлении его с углеродом выходит прочный карбид TiC с температурой плавления 3177 °С. Соединение с кремнием дает несколько видов сплавов – силициды (сплавы кремния с менее электроотрицательными металлами) Ti5Si3, TiSi и TiSi2, а также весьма плотный сплав Ti6Si3, который плавится при 2120 °С. При сплавлении титана с алюминием на выходе получаются соединения TiAl иTiAl3.
Связываясь с кислородом, титан образует несколько видов окислов – двуокись TiO2 (плавится при 1950 °С), оксид TiO (плавление при 2020 °С), и окись Ti2O3 (температура плавления 2130 °С).
Соединение железа с титаном дает на выходе два вида сплавов – TiFe (Тпл = 1317 °С) и TiFe2 (Тпл = 1427 °С). Полный состав ферротитана можно узнать из таблицы.
Ферротитан получают, главным образом, из концентратов минеральных пород, таких как ильмениты (FeOTiO2). Кроме того, титан содержится в таких минералах, как рутил TiO2, ксантитан TiO2(Al2O3)nH2O, перовскит CaOTiO2.
Состав концентрата 1 сорта включает: TiO2 – не меньше 42 %, Fe2O3 – не более 53,6 %, SiO2 – менее 2,5 %, P – не больше 0,025 %, и не более 7 % H2O. Сырье проходит предварительный окислительный обжиг, температура в печи во время процесса составляет 1100 – 1150 °С. Делается это чтобы снизить уровень серы до 0,04 %, а также для получения оксида железа при расплавлении ильменита. Такая обработка дает возможность увеличить количество используемого при плавлении титана, уменьшить потребление алюминия, а также повысить температуру процесса.
Отходы металлического титана тоже могут быть использованы для изготовления ферротитана, однако для этого они должны быть абсолютно сухими. Кроме того, подходит и титановая стружка. Для целей производства стружку прессуют в брикеты или пакетируют в железную тару.
Восстанавливают титан из отходов с помощью порошка ФС75 и крупки из вторичного алюминия. Для получения крупки алюминий в жидком состоянии распыляют сжатым воздухом или азотом, который пропускают сквозь узкую форсунку. Молотая известь с зерном менее 3 мм служит флюсом, она содержит менее 1 % углерода и более 90 % CaO.
Малофосфористая гематитовая руда (Fe2O3 – 97 %, P – менее 0,015 %), измельченная до размеров зерна в 3 мм, применяется в железотермитном осадителе. Чтобы удалить влагу, руду предварительно просушивают.